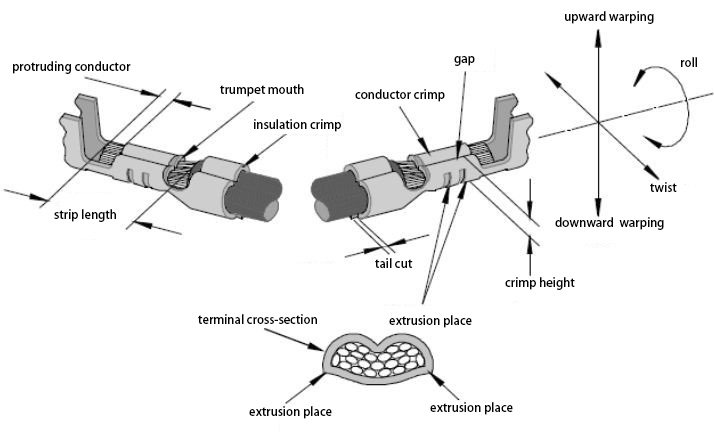
Analysis of crimping
Trumpet mouth
After crimping, a trumpet mouth is formed at the edge of the core wire crimping frame, which becomes the core wire funnel.
This funnel reduces the possibility of core wire cut off.
The thickness of the trumpet mouth should generally be about 1 to 2 times the thickness of the terminal material.
Bending test
Bending test is a method to test the crimping quality of insulation.
We bend the wire back and forth several times and then evaluate the movement of the insulation and core wire.
As a rule, the crimping of the insulation is required to withstand several 60-to 90-degree bends of the wire in any direction.
Be careful not to cut the insulation layer behind the crimping of the insulation when crimping the thin wire.
Protruding conductor
A protruding conductor is a core wire harness that passes through the core wire crimping frame and faces the terminal contact area.
Due to the existence of the core wire harness protruding from the crimping frame, the mechanical crimping force can all act on the core wire.
The conductor protrudence should not extend to the terminal plug area.
Core wire crimping
The crimping of the core wire is the compression of the terminal crimping frame on the core wire.
This operation establishes an electrical path with low resistance and high current carrying capacity.
Crimping height of core wire
The crimping height of the core wire is the distance from the crimped top surface to the bottom radial surface.
This height does not include the extrusion height (see figure above).
Crimping height measurement uses a fast and non-destructive measurement method to measure whether the terminal crimping frame around the core wire is correctly pressed to the core wire.
The measurement result is an important index in process control.
When formulating crimping height specifications, it is usually necessary to take into account the electrical and mechanical properties of crimping according to different strands, coatings, terminal materials and electroplated conductors.
Although the optimal crimping height can be determined for different strands and terminal plating, only one crimping height is generally specified.
Tail cutting
After the terminal is separated from the bearing belt, the terminal head is not flat but protruding, which is called tail cutting.
As a rule, the tail-cutting length should be 1.0 to 1.5 times the thickness of the terminal material (please refer to the specific terminal specifications).
If the tail is cut too long, the terminal (due to poor insertion) will be exposed outside the plastic shell of the connector, or can not meet the electrical spacing requirements.
In general, a tool can be set so that the cut tail is flush with the thickness of a material.
Extrusion (outreaching)
Crimping causes the bottom of the wire crimping frame to form abduction, which is caused by the gap between the punch and the anvil.
If the anvil is worn or the terminal is overcrimped, the bottom of the terminal will be overextended.
If there is a dislocation between the punch and the anvil, if the feeding adjustment function is turned off, and if the distance of the terminal being dragged is not enough or too large, there will be an uneven extrusion effect.
Insulation crimping (relieving stress)
The crimping of the insulation can provide support for the wire so that the wire can be inserted into the plastic shell.
It also helps the terminal to resist vibration.
The terminal must hold on to the wire as firmly as possible, but must not penetrate the insulation and touch the core wire.
The criterion for judging whether the crimping of the insulation is qualified or not is subjective and depends on the occasion in which the connection is used.
For specific applications, we recommend that you carry out corresponding bending tests to determine whether the stress relief provided by the crimping of the insulation is qualified.
Crimping height of insulation
The crimping height of the insulation is usually not specified because of the existence of a variety of insulation thickness, materials and hardness.
Most terminals are designed to accommodate wires of various specifications.
Terminals within its scope of application may not be able to fully hold the insulation, or may not be able to hold the wire tightly.
However, in this case, the insulation crimping is usually qualified.
1. If the wire is too thick, the insulated crimping wireframe should cover at least 88% of the wire.
2. If the wire is too thin, the insulated crimping wireframe should hold on to at least 50% of the wire and hold the head of the wire firmly.
To check the crimping section of the insulation, cut the wire from the back of the terminal so that the section is flush behind the terminal.
After determining the best crimping setting, record the crimping height of the insulation.
The operator can check the crimping height of the insulation as part of the setting step.
End position of the insulation
The end position of the insulation is in the transition zone between the insulation crimping and the core wire crimping.
In this transition zone, the length of the core wire should be the same as the length of the insulation.
The end of the insulation should be positioned to ensure that there is an insulation under the entire crimping wireframe. On the other hand, the insulation shall not extend below the crimping wireframe of core wire.
If the table crimping machine is used, the end position of the insulation is determined by the wire stop and stripping length.
If crimping with an automatic machine, the end position of the insulation is determined by the input / exit adjustment of the crimping machine.
Stripping length
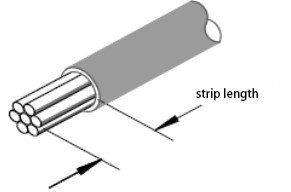
Stripping length is the core wire length exposed after the insulation of the wire is stripped off.
When the end position of the insulation is in the middle of the transition zone between the insulation crimping and the core wire crimping, the stripping length determines the length of the protruding conductor.