Technical Requirements for Cross-section of Automobile Low Voltage Wire Harness
Automobile wire harness is one of the products with rapid development, the greatest market demand and convenient installation in the electronic and information age.
The configuration function in the car is complete, but the electrical circuit hidden inside the car body is complex, the size is too large, and it is not easy to replace.
The reliability of wire harness is a key component that affects the performance of the whole vehicle, so it is necessary to control the quality of wire harness.
The requirements of the national standard for the cross-section analysis technology of automobile low-voltage wire harness and the cross-section analysis technology of crimping connection are as follows:
The connection between the terminal and the wire should give priority to the crimping terminal cross-section analysis technology, and the connection should meet the following requirements: the terminal should be crimped on the conductor and insulation layer respectively. The conductor should not be broken, the insulation layer should not press the conductor crimping position. The wire conductor should be visible, but it can not hinder the insertion.

Analysis of the cross section of the crimped terminal of the automobile wire harness shall be taken after not less than 3 cycles of bending test.
The cross section of the crimped terminal and wire should meet the requirements of the connector metallographic analysis system.
Wires of different circuits, wires of different voltages, different AC wires and DC wires cannot be in the same protective tube.
Because the uses and specifications of different lines are different, the electricity load is also different, if assembly together, the larger power load will interfere with and damage the lines with less electric charge, in case the power cord is fused, it will cause short circuit, sparks and cause fire.
Weak telecommunication lines can not go together with strong electricity, because the electromagnetic field produced by strong electricity will affect the signal of weak electricity, and lead to bad communication and video effect.
The cross-sectional area of lighting line and socket line is different, the load is not uniform, and the socket line is used frequently, which will cause electric shock, short circuit and so on.
Therefore, wires with different uses and functions must not be in the same guard tube.
Arrangement and Processing of Automobile Wire Harness Cable Assembly
The wire harness diagram should be drawn before arranging the wiring harness, which is different from the circuit schematic diagram.
The circuit schematic diagram is an image describing the relationship between the electrical parts. It does not reflect how the electrical components are connected to each other, and is not affected by the size and shape of the electrical components and the distance between them.
The wire harness diagram must not only take into account the size and shape of the electrical components and the distance between them, but also reflect how the electrical components are connected to each other.
After the wiring harness factory makes the harness wiring board according to the diagram, it cuts and arranges the wire according to the regulations of the wiring board.
The main wire harness of the whole car is generally divided into engine (ignition, electric injection, power generation, start), instrument, lighting, air conditioning, auxiliary electrical appliances and other parts, with main wire harness and branch wire harness.
A main wire harness has multiple branch wire harnesses, just like tree poles and branches.
The whole car wire harness often takes the dashboard as the core part, extending back and forth.
Due to length or convenient assembly, the wire harness of some cars is divided into front wire harness (including instrument, engine, front light assembly, air conditioner, battery), rear wire harness (taillight assembly, license plate light, suitcase light), tent roof wire harness (door, headlight, stereo speaker) and so on.
Each wire harness is marked with numbers and letters to indicate the object to which the wire is connected, and when the operator sees the sign, he can correctly connect it to the corresponding wire and electrical device, which is especially useful when changing the wire harness.
At the same time, the color of the wire is divided into monochromatic line and bicolor line, and the use of the color is also stipulated, which is generally the standard set by the car factory.
China’s industry standards only stipulate the main color, such as single black for ground lines and red monochrome for power lines, which should not be confused.
The wire harness is wrapped in woven thread or plastic adhesive tape. For safety, processing and maintenance convenience, the woven thread package has been eliminated and is now wrapped in sticky plastic tape.
The connection between wire harnesses, and between wire harness and electrical parts, adopts coupling plug-in or wire lug.
The connectors are made of plastic and are divided into plugs and sockets.
The connection between the wire harnesses is done by a coupling plug-in, and the connection between the wire harness and the electrical parts is connected by a coupling plug-in or wire lug.
Therefore, the advanced automobile introduces the CAN bus configuration and adopts the multiplex transmission system.
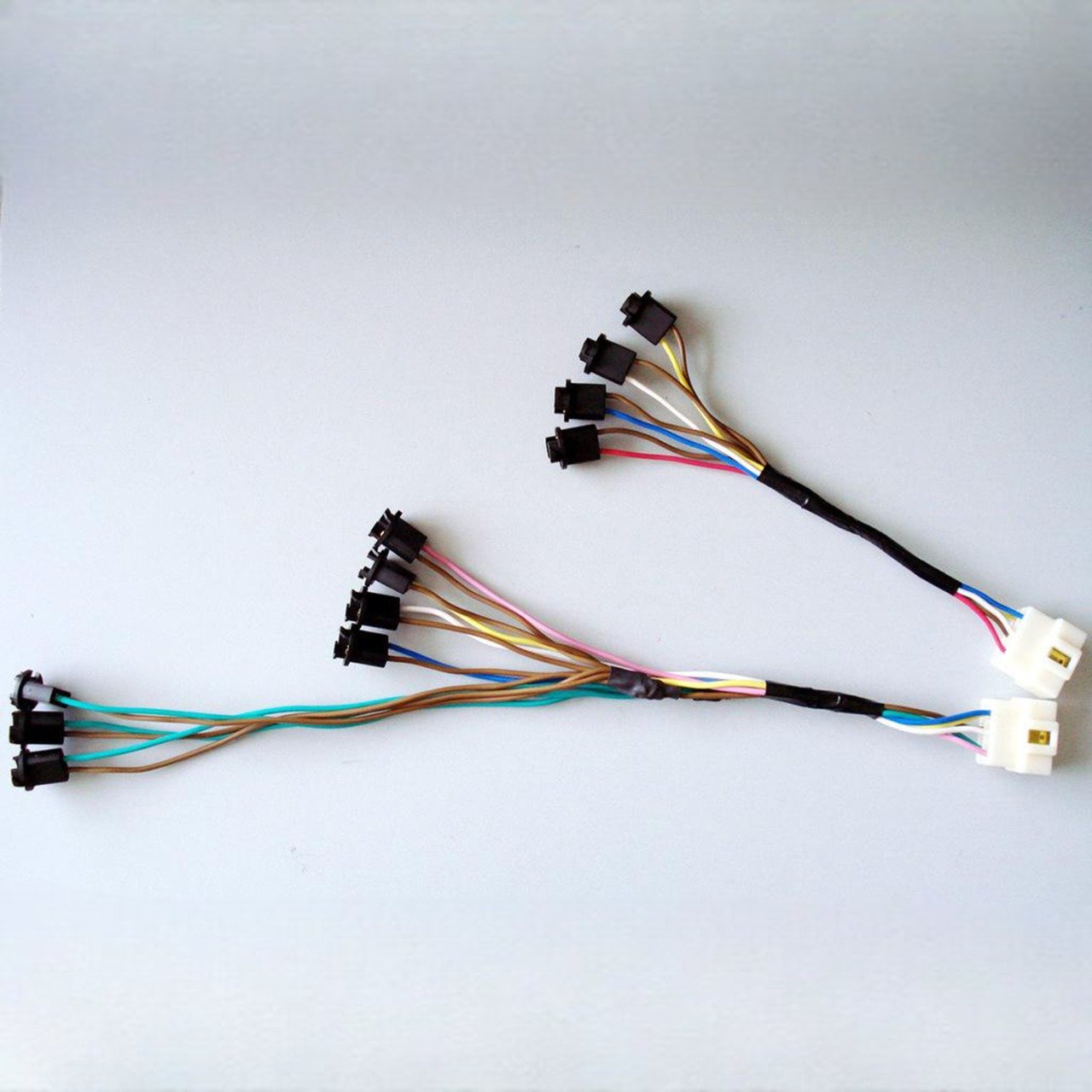
Compared with the traditional wire harness, the multiplex device greatly reduces the number of wires and connectors, which makes the wiring easier.
The conductor of automobile wire is twisted by many copper strands, and the stranded conductor has good bending and flexibility.
The copper wire of the stranded conductor is drawn by using a wire drawing machine to draw a very thick copper rod through multiple channels.
The size of the copper wire is about 0.1~0.4mm, which is about the same thickness as the hair.
The traditional wire drawing machine can only draw one copper wire at a time, and the copper wire drawn by the single wire drawing machine is drawn at different time and different equipment, and its process conditions are very different. Die, lubrication, drawing force, toughening temperature and time and other process parameters are difficult to keep consistent, such copper wire together, its size, material, metallographic structure, mechanical elastic modulus, ultimate elongation at break are very different.
At present, the advanced wire drawing machine is a multi-head wire drawing machine with continuous annealing, which can draw a bunch of copper wires at a time, which has more than ten copper wires.
This kind of wire drawing machine has the advantages of small area, high production efficiency, remarkable energy saving, less manpower and low labor intensity.
Multi-head wire drawing technology is widely used by foreign automobile wire manufacturers, mainly because it ensures the high quality of automobile wires.
Selection of Wire Materials for Automobile Wire Harness
Copper core polyvinyl chloride (QVR) and copper core polyvinyl chloride-butadiene chloride composite insulated low voltage wire (QFR) are generally used for automobile wire harness materials. While polyvinyl chloride (OVR-105) with copper core heat resistance of 105C is used in vehicle electrical and instrument lines in high temperature zone.
Delphi has developed recyclable halogen-free (Halogen Free) wire harness materials, which is a major breakthrough in the development of power wire technology in the past 30 years.
The halogen-free wire harness is coated with “flexible Noryl resin” of GE High-tech Materials Co., Ltd.
Flexible Noryl resin does not contain halogen, chlorine and lead, the highest service temperature is 110C, and the temperature characteristic and flame retardancy are excellent.
More importantly, this material is very environmentally friendly and can be recycled.
The color of the wire harness: the bus wire harness is intricate.
In order to facilitate wiring and repair, it should be able to visually distinguish the wire head, and the wires of the same diameter in the same bundle should be distinguished in color as far as possible.
The color of the wire harness can be divided into monochrome or bicolor. The bicolor is composed of the primary color and the secondary color, and the secondary color is distributed symmetrically, and the arrangement method is the primary color before the auxiliary color, such as the red-green wire (RG);
The color and code of the monochromatic sign are red R, orange O, yellow Y, green G, brown N, blue U, purple P, black B, white W, gray S.
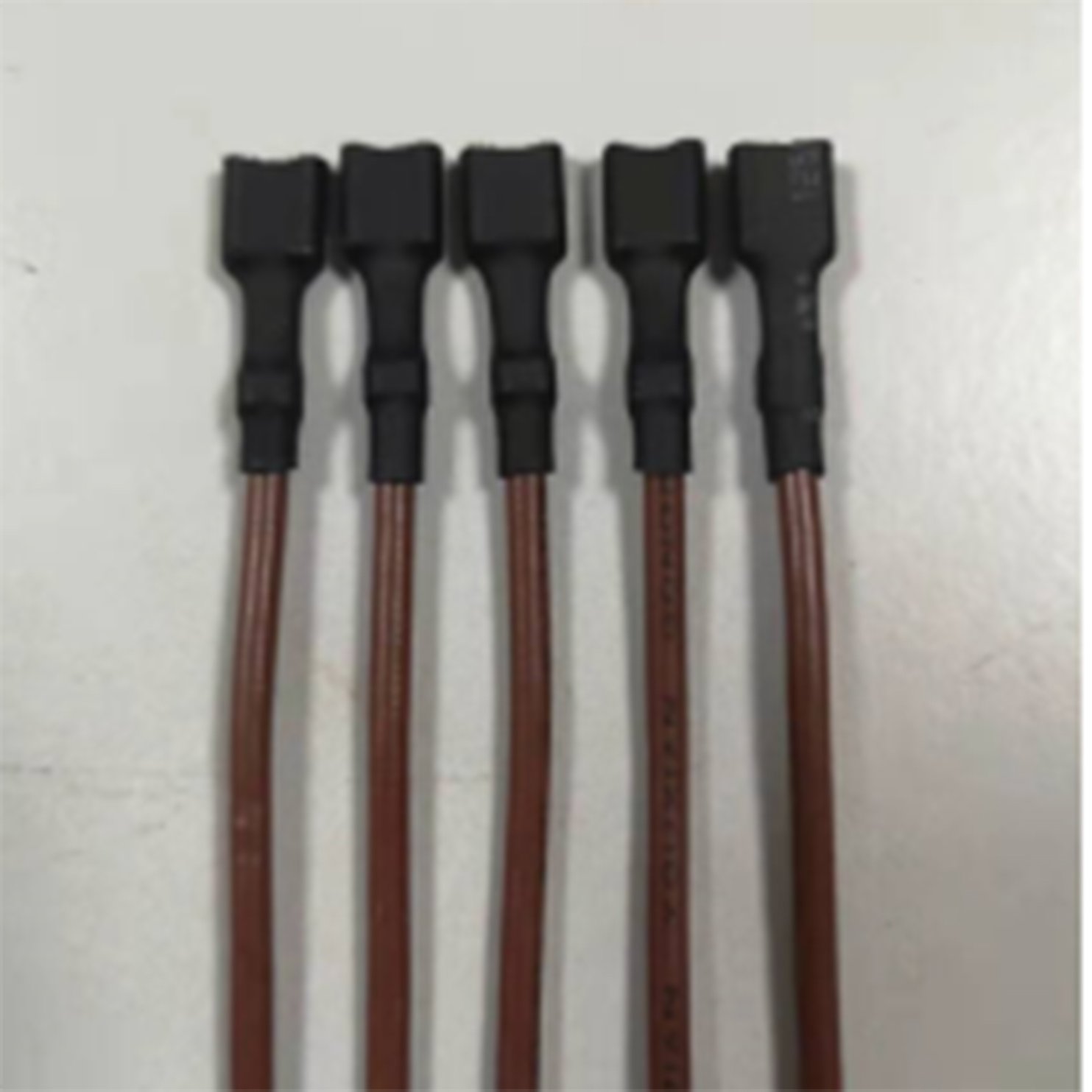
Wire and cable as the main carrier of power transmission, when selecting and purchasing automobile cable, we should pay attention to the following points.When selecting and purchasing wire and cable products, we should observe whether the product qualification certificate is complete with regard to the product type, specification, rated voltage, number of cores, production date, implementation standard, license number and other related information, and the continuity marks of factory name, product model and rated voltage should be printed on the physical surface of the product.
Verify that the information related to the two is consistent.
The outer plastic insulation of the wire is bright in color and fine in texture. There are no burrs or protuberances on the surface. The appearance is smooth, round and uniform. The conductor uses electrolytic copper, and the outer layer is bright and slightly soft.
If you look at the cross section of the cable, the copper (aluminum) core should be in the middle and the thickness of the plastic layer should be uniform.
There is a length mark on the certificate, you can first estimate the length of the coil of the finished product package, then count the number of coils, estimate the approximate length of the whole coil, in addition, pay attention to the diameter of the conductor, look at the length and section of the cable.
When selecting wire and cable products, it is best to consult experienced professional electricians to adopt cables with appropriate cross-section size and voltage level according to their own electricity load.
Concluding Remarks
To sum up, with the increase of automobile functions and the widespread application of electronic control technology, there are more and more electrical parts, more and more wires, and the wire harness becomes thicker and heavier.
Modern automobile introduces CAN bus configuration and adopts multiplex transmission system.
Compared with the traditional wire harness, the multiplex device greatly reduces the number of wires and connectors, which makes the wiring easier.