2.4 Principles of fixing automobile wiring harness
The overall layout and fixing of the automobile wire harness need to ensure simple operation and convenient maintenance, so as to avoid the problem of disassembling and assembling other parts of the vehicle or maintenance.
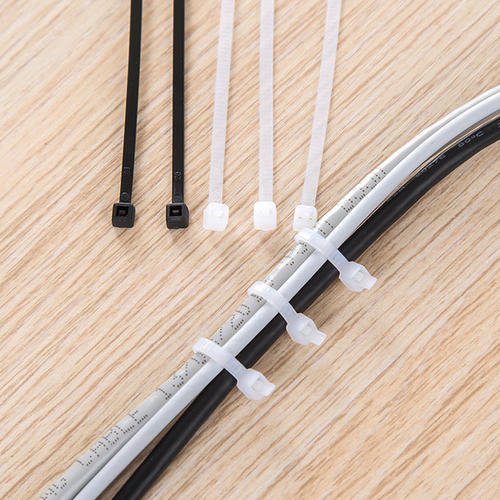
1). In the assembly of automobile low-voltage wire harness, the fixed device corresponding to every 200~300mm distance can be increased appropriately in special harsh environment, but the distance should not be greater than 150mm.
2). When fixing the inflection point of the wire harness, two are usually used at the right angle and one at the obtuse angle. The acute angle direction of the wire harness is not recommended.
3). When the installation position of the connector is less than 120 mm, it is necessary to increase the fixed point to reduce the damage to the wire harness caused by the vibration.
4). If the wiring harness installation area fixing device is missing, it is necessary to design devices such as wire harness fixing along the slot or bracket separately.
It should be noted that the gap between the wire harness and the automobile parts without sharp edges is above 6mm (including), and the parts with sharp edges are at least above 30mm.
5). In automobile wiring harness, if the wiring harness is long, the excess needs to be fixed or bundled separately, and the minimum bending radius should not be less than 2 times the diameter of the wiring harness.
To sum up, when the automobile wire harness is assembled, it is necessary to ensure the smooth direction of the wire harness, fixed device, reasonable position and so on.
2.5 Layout of high voltage wiring harness for new energy vehicles
2.5.1 Characteristics of high voltage wire harness
The high-voltage wire harness needs to carry a high voltage of 60 to 1500V, which is one of the key components of the high-voltage system of new energy vehicles, which can provide high voltage for new energy vehicles and drive the vehicle with high voltage and high efficiency.
High-voltage wire harness has the characteristics of high voltage, strong current, thick and large wire diameter, so the layout design of high-voltage wire harness of new energy vehicles is faced with many challenges.
The high-voltage wire harness generally works continuously under the condition of high voltage and strong current, if the heat dissipation of the high-voltage wire harness is not timely, the automobile wire harness is easy to catch fire, which puts forward higher requirements for the heat resistance of the wire harness. As there are high-voltage electrical components in new energy vehicles, other low-voltage electrical parts are very easy to produce electromagnetic interference when the voltage changes, so the anti-electromagnetic interference of high-voltage wire harness also needs to be specially designed.
In addition, the high-voltage wire harness is expensive and takes a long time to replace, so the service life of the high-voltage wire harness needs to be optimized to ensure the long-term safe use of new energy vehicles.
2.5.2 Optional design of high voltage wire harness
Compared with the low-voltage wire harness, the main difference between the high-voltage wire harness and the low-voltage wire harness is that the protective layer of the high-voltage wire harness is higher than that of the low-voltage wire harness, and the metal layer structure is needed for protection, and other structures are consistent with the low-voltage wire harness. It mainly includes cables, connectors and protective structures.
Among them, the wire harness connector of high voltage wire harness has higher requirements for current bearing capacity, conductivity and resistance to electromagnetic interference, and generally requires a larger connection area. It has the ability of corrosion resistance, high and low temperature resistance, and can be plugged and unplugged many times to ensure the stable connection characteristics and conduction capacity of the high voltage wire harness.
The protection of high voltage wire harness also needs special consideration, especially the protection against electromagnetic interference. Common protective structures include bellows, tape, protective joints, metal braided mesh and so on.
Other protection and fixing devices of high-voltage wire harness are basically the same as low-voltage wire harness, and try their best to stay away from low-voltage wire harness and low-voltage parts.
2.5.3 Principle of high voltage wire harness layout
1).When the new energy vehicle is working normally, the current of its high voltage system is as high as tens of amperes or even higher, and the current will increase exponentially during instantaneous discharge. Therefore, the design and layout of high voltage wire harness needs to fully consider the safety of vehicles and personnel. It is necessary to explain the design and layout of the high voltage wire harness.
The cable of the new energy vehicle can not be exposed, and its cables and connectors must be designed in orange to be easily distinguished from conventional low-voltage electrical components such as low-voltage wire harness, so as to avoid accidents caused by personnel misoperation.
The cable should be protected by bellows and heat-shrinkable tubes, in which bellows, connectors, tape and jackets all use orange. For heat-shrinkable pipes, different colors need to be used to distinguish electrodes, positive electrodes is red, negative electrodes is blue, U phase is yellow, V phase is green, W phase is red.

2).The high-voltage wire harness itself is reasonably arranged, and the power supply system should be set up separately to prevent the phenomenon that the non-working parts of the high-voltage parts are still electrified.
3). The high-voltage wire harness should be arranged away from the fuel line, leaving at least a 100mm distance if it needs to be close to the fuel line.
4). The parallel distance of automobile high and low voltage wire harness is greater than 400mm. If this distance cannot be realized in the actual environment, it is recommended that the high and low voltage wire harness should be vertical to avoid electromagnetic interference.
5). The small bending radius of the high-voltage wire harness is avoided when the high-voltage wire harness is arranged, and the minimum bending radius of the wire harness is usually more than 5 times of the outer diameter of the wire harness. It is necessary to pay attention to the high-voltage wire harness to avoid the exposure of the joint, otherwise it is very easy to cause leakage due to seal failure.
6). After the completion of the arrangement and installation of the high-voltage wire harness, it is recommended to add protective devices to prevent pollution and damage to the high-voltage wire harness by the external environment.
7). Considering that the high-voltage wire harness connector is large, the wire harness insertion or connection part should set aside the appropriate length, the length is not less than 200mm, and enough space should be set aside to ensure convenient assembly and maintenance.
3 Concluding remarks
The layout and application of automobile wire harness has more and more important influence on automobile reliability, so it is necessary to arrange automobile wire harness scientifically and rationally.
When laying the automobile wiring harness, it is necessary to combine the actual situation of the automobile to ensure the safety and reliability of the automobile wiring harness.
The wiring harness of new energy vehicles is layout scientifically and rationally, so as to provide strong support for the safe and stable operation of new energy vehicles.