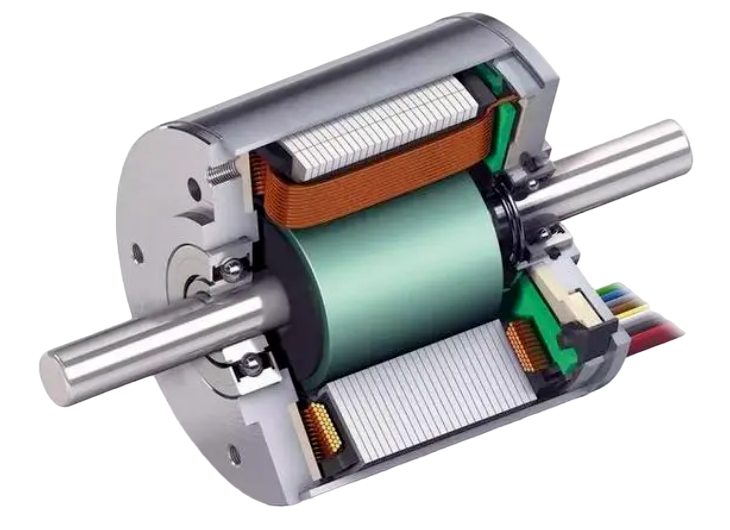
3. NVH advantages of flat wire motor
The special performance requirements of new energy vehicle drive motor are mainly reflected in high power density, wide efficiency range, wide speed regulation range, large starting torque, strong heat dissipation demand and so on.
Therefore, the development trend of new energy vehicle drive motor will also focus on these performances. At present, several mainstream directions are flat wire motor, oil-cooled motor and all-in-one electric drive assembly.
The flat wire motor has higher power density, the gap between the flat copper wire is large, and the cooling oil is easy to permeate. The development of the flat wire motor promotes the application of direct oil cooling technology.
At the same time, the cooling oil has good insulation and can be used as lubricating oil for reducers and gear bearings, and the waste heat of the motor can also be collected for the heat preservation of the battery package. The direct oil cooling technology accelerates the process of the integration of the vehicle thermal management system and promotes the development of the all-in-one electric drive system assembly.
The flat wire motor refers to replacing the traditional cylindrical enamelled copper wire in the stator winding with a hairpin-shaped enamelled copper wire.
In the cross section of the stator winding of the round wire motor, there are a lot of gaps between the round copper wire, while in the cross section of the stator winding of the flat wire motor, the rectangular copper wire can better fill the space and improve the slot full rate, which is the essential difference between the flat wire motor and the round wire motor.
Compared with the round wire motor, the primary advantage of the flat wire motor is the reduction of loss and the improvement of efficiency.
Among the losses of the permanent magnet synchronous motor, the copper consumption (mainly the loss in the stator winding) accounts for about 65%, the iron consumption (the loss in the stator core and the rotor core) accounts for about 20%, and the remaining losses account for a relatively low proportion.
The iron consumption level of flat wire motor and round wire motor is the same, and the main difference lies in copper consumption.
Copper consumption can be divided into DC loss and AC loss.
Both round wire motor and flat wire motor have DC loss. When the current phase number and current effective value are given, the DC loss is proportional to the DC resistance of the winding.
Because the round wire is thinner and the resistance is higher, the DC loss of the round wire motor is usually higher than that of the flat wire motor under the same conditions.
Because the cross-section size of single winding of round wire winding is small, the AC loss can be ignored, while the AC loss of flat wire winding is relatively large because of its large cross-section size and affected by skin effect and proximity effect.
In addition to improving the efficiency and reducing the loss, the flat wire motor has a larger efficiency range, higher power density, stronger heat dissipation capacity and better NVH performance than the round wire motor.
From the source analysis, the same power, lower copper loss and iron loss are greatly reduced, and higher efficiency also means lower radial force amplitude of each order, which indirectly brings the overall reduction of the main radial force of the whole NVH. The flat wire motor needs to be embedded from the notch and plugged in directly through the end of the iron core, which means a smaller slot design, that is, a smaller cogging torque.
Higher stator stiffness: the higher the winding stiffness of the flat wire motor, that is, to improve the overall, especially the stator stiffness, the same radial force wave, the smaller the vibration amplitude of the shell, the smaller the radiated noise.
New energy vehicles have higher and higher requirements for mileage, power density and energy efficiency, and the electric drive system is gradually developing in the direction of integration, miniaturization and lightweight.
At present, the released multi-in-one electric drive system includes three-in-one, four-in-one, six-in-one, seven-in-one or even eight-in-one electric drive system, of which the most common one is three-in-one electric drive system.
The “multi-in-one” integration scheme of the electric drive system can share circuits and power semiconductors, reduce the amount of cables, effectively reduce the volume and weight of the electric drive system, increase the power density, and realize lightweight.
It plays a more effective role in the NVH control of the motor assembly.
4 Development process of NVH for drive motor
The general motor NVH development process consists of eight parts.
They are design requirements, topology design, electromagnetic design, simulation analysis, A prototype, rectification optimization, B prototype, vehicle matching.
1). In the design requirement stage, according to the performance requirements, determine the motor performance parameters and NVH performance indicators for the bidding products.
2). The topology design stage confirms the motor type, rotor structure, length-diameter ratio, slot number and their influence on NVH.
3). In the stage of electromagnetic design, the geometric dimensions of the motor, pole-slot fit, winding, material selection and their influence on NVH, cogging torque analysis, etc.
4). The simulation analysis stage includes electromagnetic simulation, structural simulation, multi-physical field simulation and balancing other performance indicators.
5). A prototype stage carries on the prototype bench NVH test, the verification simulation result, the structure mode test, and the noise source identification test.
6). Electromagnetic scheme optimization, structure scheme optimization, performance balance and optimal scheme selection are carried out in the rectification and reform optimization stage.
7). In the B prototype stage, the optimized prototype is checked and accepted by bench NVH, loading NVH verification, achieving the single target and so on.
8). Vehicle test verification, mounting design, acoustic package development, and target confirmation are conducted in the whole vehicle matching stage.
5 Conclusion
This paper introduces the development status of the new energy driven motor industry, and discusses in detail the structure, working principle and noise mechanism of the mainstream motor in the industry: permanent magnet synchronous motor (PMSM). The torque ripple and radial force wave causing electromagnetic noise of PMSM are described in detail, the NVH performance advantages of flat wire motor are introduced, and the NVH development flow and noise simulation flow of PMSM are established.
It provides a direction for the development of NVH for driving motor.