Preface
Compared with the wire harness in traditional vehicles, the new energy vehicle wire harness not only includes the ordinary vehicle wire harness that transmits electrical signals and the electric energy needed by the operation of low-voltage equipment, but also the high-voltage wire harness is an indispensable and important component.
The high-voltage wire harness in new energy vehicles undertakes the important mission of safely and reliably transmitting the electric energy needed to drive vehicles, and plays a key and important role in the safety, reliability and stability of new energy vehicles.
According to the statistical analysis of the China Association of Automobile Manufacturers, in September 2022, new energy vehicles continued to maintain rapid growth, with monthly production and sales reaching a record high, with a market share of 27.1%.
From January to September in 2022, the production and sales of new energy vehicles reached 4.717 million and 4.567 million respectively, an increase of 1.2 times and 1.1 times over the same period last year, with a market share of 23.5%.
Behind the prosperous market, in addition to the strong policy support, the continuous development of new energy vehicle technology is also an important driving force.
Among the core technologies of new energy vehicles, in addition to the three-electricity technology, which has been widely discussed, as the high-voltage wire harness of the “main artery” of new energy vehicles, as the market pays more and more attention to the safety and reliability of new energy vehicles, it has been paid more and more attention by the industry.
High Voltage Wire Harness in New Energy Vehicles
As one of the cores of the new energy vehicle, the power battery provides energy for the vehicle directly or indirectly; the drive motor uses the power provided by the power battery to drive the vehicle; the electronic control system mainly manages the power output of the drive motor.
These devices are connected to achieve their respective functions, that is, all kinds of wire harnesses installed on new energy vehicles.
Compared with the wire harness in traditional vehicles, the new energy vehicle wire harness not only includes the ordinary vehicle wire harness that transmits electrical signals and the electric energy needed by the operation of low-voltage equipment, but also the high-voltage wire harness is an indispensable and important component.
The high-voltage wire harness in new energy vehicles undertakes the important mission of safely and reliably transmitting the electric energy needed to drive vehicles, and plays a key and important role in the safety, reliability and stability of new energy vehicles.
In new energy vehicles, high voltage harness is divided into: power battery high voltage cable (connecting power battery and high voltage box), motor controller cable (connecting high voltage box and motor controller), fast filling wire harness (connecting fast filling and high voltage box), high voltage accessory wire harness (connecting high voltage box to DC/DC, air conditioner, etc.).
Compared with traditional vehicles, power battery high voltage cable, motor controller cable and fast charging wire harness are new applications of high voltage wire harness in new energy vehicles.
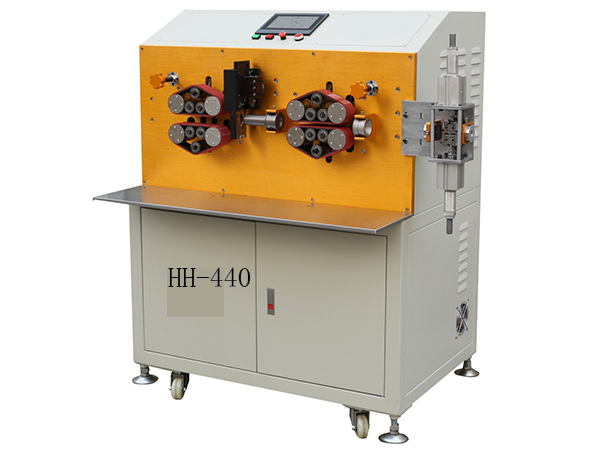
HH-440 https://youtu.be/0zUIUSNqzxM 120 sqmm new energy
In order to meet the special requirements of new energy vehicles, the technical requirements of high voltage wire harness for new energy vehicles are more comprehensive and strict, especially for high voltage and high current modules, because of the requirements of high power, interior space and wiring design, it needs to have the characteristics of high current resistance, high temperature resistance, flame retardancy, high flexibility and EMC shielding performance to meet the safety and power requirements of new energy vehicles.
For example, in pure electric new energy vehicles, the power supply voltage is generally more than 300 V and the current can reach 500 A, so the high voltage wire harness is required to have a higher temperature resistance grade, generally at-40 ℃ ~ 125 ℃, and some parts need to reach 150 ℃. Secondly, the allowable temperature rise of the high voltage wire harness is not more than 55 K to ensure that the temperature is stable within the safe range when working at high current.
In addition, the wire diameter of the high voltage wire harness is large, and when the working current reaches 500A, the wire diameter of the single core wire needs to reach 135A, and the thicker wire harness will cause the bending stress to increase, and the insertion force of the connector will also increase when the wire harness is installed.
If the high voltage wire harness material has certain flexibility, it will help to counteract the bending stress and improve the reliability of the connection between the wire harness and the connector.
At the same time, in order to ensure the safety of waterproof and leakage, the level of protection required by the connector is greater than IP67, and in order to prevent electromagnetic interference caused by high current, high-voltage wire harness also requires electromagnetic shielding, generally requiring copper wire braided shielding coverage density ≥ 85%, braided copper wire diameter > 0.1 mm.
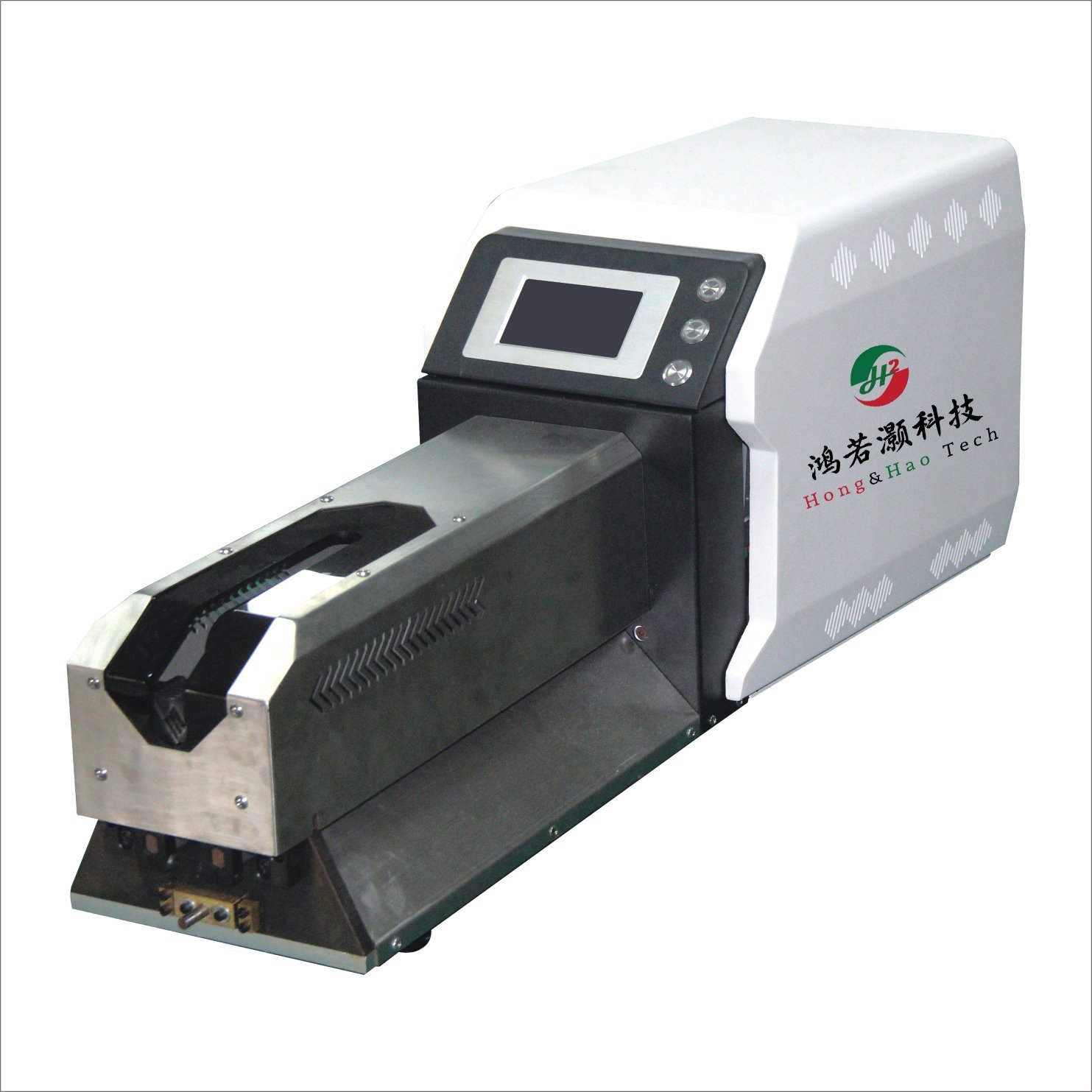
It should be noted that with the increasing popularity of 800V system, the technical requirements of high-voltage wire harness will be further improved, which will bring new challenges to the layout of vehicle wiring harness.
First of all, the challenge to be faced is that the larger cross-section of the high-voltage wire harness will bring difficulties in wiring, and it is generally required that the turning radius of the high-voltage wire harness should be more than 6 times the diameter of the high-voltage wire harness; secondly, the layout of the high-voltage wire harness needs to consider electromagnetic compatibility (EMC) and interference sources, and the high-voltage connection wire harness is recommended to stay away from the easily interfering parts and its connection wire harness, preferably separately.
The distance between the high-voltage wire harness and the connecting wire harness of the easily interfering parts should be more than 10 cm. At the same time, the electromagnetic interference can be effectively reduced by arranging the wire harness in the grooves and angles of the metal body, or close to the metal body.
To sum up, with the improvement of the technical requirements of high-voltage wire harness for new energy vehicles, how to control the working temperature rise of high-voltage wire harness and reduce the cross-sectional area of high-voltage wire harness as much as possible under the condition of carrying capacity, this is of great significance for the safe use of high-voltage wire harness in new energy vehicles and the layout of interior space.
In order to meet the working temperature rise of high voltage wire harness and optimize the layout of high voltage wire harness, the material selection of high voltage wire harness must be considered.
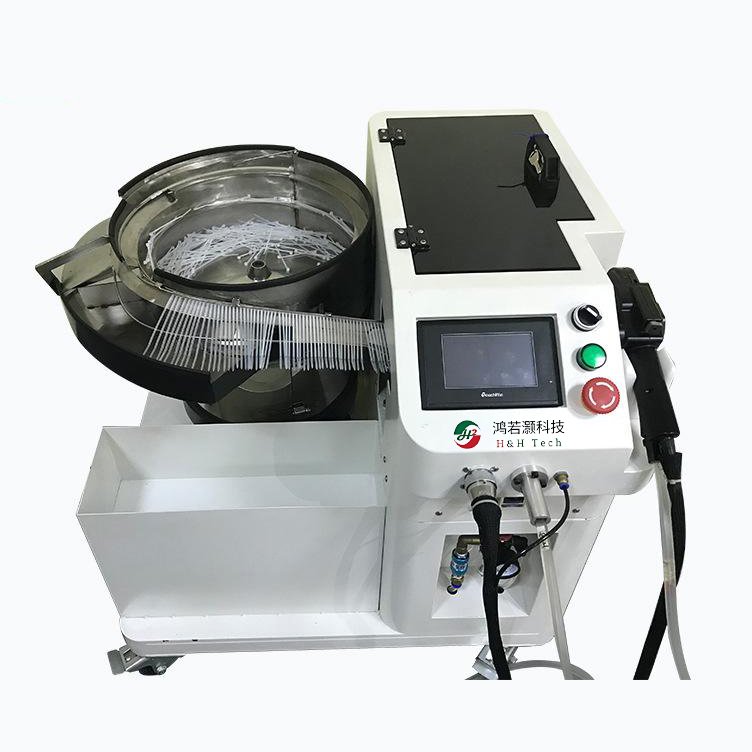
At present, the automotive high voltage wire harness is mainly made of copper as conductor (see QC/T1037-2016), including bare round copper wire and tinned soft round copper wire.
Copper material has excellent electrical conductivity (the resistance of copper is 0.0185 Ω mm²/m and that of aluminum is 0.0294 Ω mm²/m at 20 ℃).
In the case of high current, the working temperature rise is lower, on the one hand, it can reduce the heat loss during transmission; on the other hand, the excellent thermal conductivity of copper material also ensures that the working temperature of the high voltage wire harness is stable in the safe range.
At the same time, due to its excellent electrical conductivity, the cross-sectional area of copper wire can be smaller under the same load, which can effectively help the flexible arrangement of high voltage wire harness, including a smaller turning radius (the turning radius of high voltage wire harness generally needs to be more than 5~6 times the diameter of the wire harness).
In addition, the thinner wire harness can reduce the bending stress, and when installing the wire harness, the insertion force of the connector is smaller, which helps reduce the difficulty of installation and maintenance, and improve the stability and reliability of assembly; moreover, a smaller cross-sectional area can help the high-voltage wire harness to be flexibly arranged in grooves and angles that fit the metal body, or close to the metal body arrangement to effectively reduce electromagnetic interference.
In addition to good electrical conductivity, another advantage of copper as a high-voltage wire bundle conductor is its good tensile strength and bending properties.
Copper has good mechanical properties, tensile strength 200-240MN/M2 and elongation up to 50%. Its good plasticity makes it easy to process and has high plastic deformation ability. Products of various shapes and sizes can be made by pressure processing methods such as Calendering, extrusion and stretching, while the high voltage wire harness with copper as conductor can withstand vibration and friction during vehicle driving.
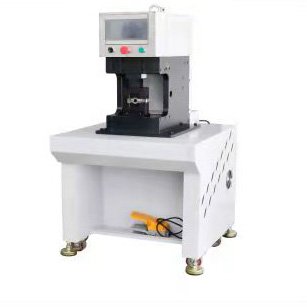
It has higher reliability and longer service life.
Copper also has good chemical stability, good corrosion resistance and easy welding. The operating environment of the vehicle is complex and harsh, and the high-voltage wire harness and terminal joints will inevitably work in damp, salt fog and other corrosive environment.
According to the experience of traditional automobile wire harness, in the environment of humidity, high temperature and vibration, such as friction and collision with other components, it is easy to cause insulator wear, joint loosening, wire corrosion and so on, and then lead to open circuit or short circuit and other faults.
Because the high-voltage wire harness carries higher voltage, greater current, and greater stress on terminals and connectors, the safety requirements are higher, and conductor materials are required to have better chemical stability.
The Balance between Safety and Lightweight of High Voltage Wire Harness
Safety is the most important index of high-voltage wire harness. The safety design of high-voltage wire harness is mainly reflected in insulation, voltage protection, overload, connector IP grade, equipotential balance, high-voltage wiring layout and so on.
From the point of view of safety, the use of materials with better electrical conductivity and thermal conductivity is beneficial to optimize the energy efficiency of high voltage wire harness and reduce the working temperature rise. The use of materials with better tensile strength and plasticity helps to improve the reliability of high voltage wire harness in the case of vibration and friction during production, assembly and vehicle operation, and is conducive to optimizing the spatial layout of the wire harness.

The use of materials with more stable chemical properties can prevent corrosion, ensure good contact between the high voltage harness terminal and the connector, and reduce the safety risk caused by poor contact.
Lightweight is the common concern of both new energy vehicles and traditional vehicles, and high-voltage wire harness is an important field of lightweight of new energy vehicles.
Lightweight helps to improve energy efficiency, increase the mileage of new energy vehicles, and reduce costs appropriately.
However, when considering the lightweight scheme, it is necessary to ensure the security of the system, and comprehensively consider the whole system risk and the whole life cost.
First of all, any lightweight scheme can not be at the expense of increasing security risks, but needs to be lightweight within the scope of security.
Secondly, lightweight design should not only consider the local optimization, but also comprehensively consider the lightweight and cost of the whole vehicle system.
For example, for the lightweight of high-voltage wire harness materials, we need to consider not only the changes to the wire harness itself, but also its impact on terminals and connectors, changes in electromagnetic shielding, and the impact on system maintenance in the future vehicle life cycle.
In short, as the blood vessels and nervous system of new energy vehicles, high-voltage wire harness has an impact on the whole body of new energy vehicles.
The safety of high voltage wire harness is the basic guarantee for the safety of new energy vehicles, and its technical development plays an important role in improving the performance of new energy vehicles.