The automobile wire harness is the network main body of the automobile circuit, without the wire harness, there will be no automobile circuit.
With the improvement of the safety, comfort, economy and emission requirements of the automobile, the automobile wire harness becomes more and more complex, but the space given by the car body to the wire harness is getting smaller and smaller.
Therefore, how to improve the comprehensive performance design of automobile wire harness has become the focus of attention, and automobile wire harness manufacturers no longer simply engage in wire harness post-design and manufacturing, and automobile mainframe manufacturers to jointly carry out pre-development has become an inevitable trend.
Based on the experience of harness design and manufacture in recent years, the author talks about the general design and design principles of harness.
Whole Vehicle Circuit Design
1. Power distribution design
Whether the design of automobile power supply system is reasonable or not is directly related to the normal operation of automobile electrical devices and the safety of the whole vehicle, so the starting point of automobile wiring harness design all over the world is safety-oriented.
The electrical system of the whole vehicle is basically composed of three parts.
Battery direct power supply system (commonly known as constant electricity or 30 electricity).
The load connected to this part of the power supply is generally the safety or important parts of the car, and the main purpose is to control as little as possible when providing electricity for these parts, so as to ensure that these parts can work normally for a short time even if the car does not start. To facilitate maintenance at the site, etc.
For example, the working power supply of engine ECU and engine sensor, the working power supply of fuel pump, and the power supply of ABS controller and diagnostic interface, etc.
Power supply system controlled by ignition switch (commonly referred to as IG).
This part of the electrical device is basically used when the engine is running and is taken from the power supply of the generator to avoid the possibility of competing for power when charging the battery.
Such as: instrument power supply, brake light power supply, airbag power supply and so on.
Remove the power supply from the load when the engine starts (commonly known as ACC power supply).
This part of the electrical devices generally carry a large load, and do not have to work when the car starts. Generally have some smoke power supply, air conditioning power supply, radio power supply, wiper power supply and so on.
2. Circuit protection design
Circuit protection is to protect the wire, taking into account the protection of loop electrical devices. The protective devices mainly include fuses, circuit breakers and fusible wires.
A. Selection principle of fuse
Engine ECU, ABS and so on have a great influence on the performance and safety of the whole vehicle. In addition, fuses must be installed on the electrical devices that are easily disturbed by other electrical equipment.
Engine sensors, all kinds of alarm lights, external lights, horns and other electrical devices also have a great impact on vehicle performance and safety, but this kind of electrical load is not sensitive to mutual interference.
Therefore, this kind of electric load can be combined with each other according to the situation and use a fuse together.
Fuses are divided into fast fusing type and slow fusing type.
The main component of the fast fuse is the thin tin wire, in which the chip fuse is widely used because of its simple structure, good reliability and vibration resistance, and easy detection; the slow fuse is actually a tin alloy sheet, and the fuse of this structure is generally connected to the inductive load circuit, such as the motor circuit.
Resistive loads and inductive loads try to avoid using the same fuse. Generally, the fuse capacity can be calculated and determined according to the maximum continuous working current of the electrical device, according to the empirical formula: fuse rated capacity = circuit maximum working current / 80% (70%).
B. Circuit breaker
The biggest characteristic of circuit breaker is recoverability, but its cost is high and its use is less.
Circuit breakers are generally heat-sensitive mechanical devices, which make the contacts open and close or turn on by themselves by making use of the different thermal deformations of the two metals.
A new type of circuit breaker, which uses PTC solid material as overcurrent protection element, is a positive temperature coefficient resistance, which is turned on or off according to the current or temperature. The biggest advantage of this kind of protection element is that it can be turned on automatically after troubleshooting, without manual adjustment and replacement.
C. Fusible wire
The characteristic of fusible wire is that when the wire passes through a large overload current, the fusible wire can be fused in a certain period of time (generally ≤ 5s), thus cutting off the power supply and preventing serious accidents.
Fusible wire is also composed of conductor and insulating layer, the insulating layer is generally chlorosulfonated polyethylene material, because the insulating layer is thick, so look thicker than the wire of the same specification.
The fusible wire is generally connected to the circuit directly out of the battery.
The common cross sections of fusible wires are 0.3 mm², 0.5 mm², 0.75 mm², 1.0 mm², 1.5 mm², and even larger sections such as 8 mm².
The length of the conductor segment of fusible wire can be divided into (50±5) mm, (100±10) mm and (150±15) mm.
The fusible wire should be clearly marked, and when it is fused, the mark should still exist to facilitate replacement.
The fuse characteristics of fusible wires are shown in Table 1.
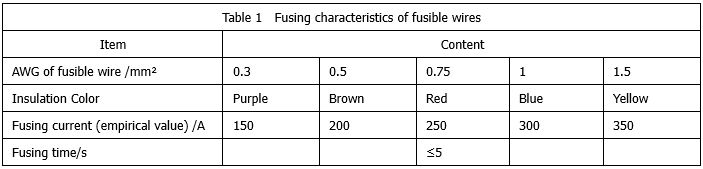
Fusing characteristics of fusible wires
3. Selection and Design of Relay
Relays are divided into current type and voltage type.
Generally, according to the power of the appliance and the carrying capacity of the switch, we decide whether to choose the relay or not.
The devices of common relay generally have wiper, horn, defrost, headlight, foglight, fan, blower, turn signal (flasher) and so on.
Relays are divided into 6V, 12V and 24V, and the rated voltage of commonly used relays is 12V. The technical requirements for the selection of relays are as follows: (1) good reliability; (2) stable performance; (3) light weight, small volume, long life, and little influence on the surrounding components; (4) simple structure, good processability and low cost.
4. Design principles of build-iron distribution
Engine ECU, ABS and other engines have a great impact on vehicle performance and safety, and are easily disturbed by other electrical equipment, so the build-iron points of these parts must be set alone.
For the airbag system, its build-iron point should not only be set up alone, but also in order to ensure its safety and reliability, it is best to use compound build-iron.
The purpose is that one of the build-iron sets fails, and the system can build iron through another iron point to ensure the safe operation of the system.
In order to avoid disturbances, the radio system should also be built separately.
The build-iron setting of the weak signal sensor should be independent, and the iron point should be close to the sensor to ensure the true transmission of the signal.
Other electrical devices can be combined with each other to build iron points according to the specific layout.
The principle is to build the nearest build-iron to avoid too long, resulting in unnecessary voltage drop.
Because of the large cross section of the negative electrode wire of the storage battery and the iron wire of the engine, it is necessary to control the length and direction of the wire and reduce the voltage drop. In order to increase safety, the engine and the car body should be connected to the negative electrode of the battery separately. The way of build-iron: one is to build iron through the hole joint, which must be insulated by heat-shrinkable tube at the end of the joint; the other is to build iron directly through the sheath of internal short connection.
Wire harness 3D layout towards design
The main purpose of this process is to simulate the direction and diameter of the wire harness in different regions, consider the sealing box protection of the wire harness through the hole, and simulate the fixed hole position and fixing mode of the wire harness.
The main software used in 3D cabling is PRO-E, UG, CATIA and so on.
Design of connector selection
The connector is the core component of wire harness, and the performance of the connector directly determines the overall performance of the wire harness, and plays a decisive role in the electrical stability and safety of the whole vehicle.
1. Selection and design principles of connectors
The selection of connectors should ensure good contact with electrical devices, reduce the contact resistance to the lowest, improve reliability, and give priority to the connectors with double-spring compression structure.
The connectors are reasonably selected according to the cross-sectional area of the wire and the passing current.
For the docking jacket in the engine cabin, due to the high temperature and humidity in the cabin and the existence of a lot of corrosive gases and liquids, the waterproof jacket must be chosen.
If the same sheath is used in the same wire harness, its color must be different.
Based on the overall coordination of the car appearance, black or dark jackets should be preferred in the engine compartment.
In order to reduce the type and quantity of sheath for wire harness docking, hybrid parts are preferred to make assembly convenient.
For terminal connectors used in airbags, ABS, ECU, etc., which require high performance, gold-plated parts should be preferred to ensure safety and reliability.
The inside of the battery joint (battery clip) is a cone with a taper of 1: 9; the battery clip is made of tin-plated copper, galvanized copper or lead-antimony alloy. The current carried by connectors of different specifications is generally as follows: 1 series, about 10A; 2.2 or 3 series, about 20A; 4.8 series, about 30A; 6.3 series, about 45A; 7.8 or 9.5 series, about 60A.
2. Performance analysis of raw materials of connectors
A.Sheath material (plastic parts)
The commonly used materials are mainly PA6, PA66, ABS, PBT, PP and so on.
When designing connectors, different materials can be selected according to different needs, and flame retardant or reinforced materials can be added to plastics according to the actual situation to achieve the purpose of strengthening or flame retardant, such as adding glass fiber reinforcement.
B. Terminal material (copper)
The copper used for connectors is mainly brass and bronze (the hardness of brass is slightly lower than that of bronze), of which brass accounts for a larger proportion.
In addition, different coatings can be selected according to different needs.