In the realm of electrical and mechanical applications, shrink tubing has emerged as an indispensable component, offering protection, insulation, and organization.
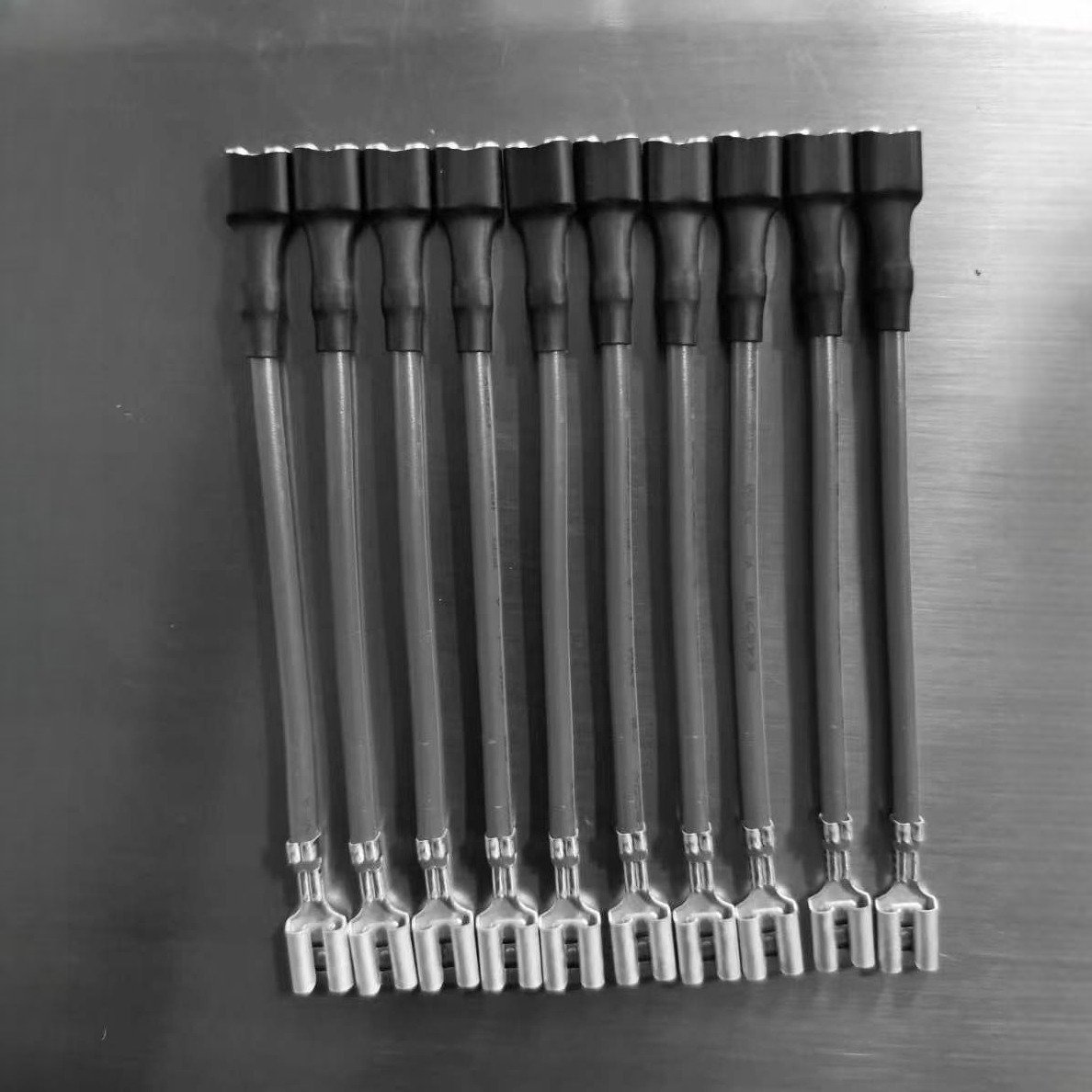
Shrink tubing, also known as heat shrink tubing, is a flexible polymer tube that shrinks in size when exposed to heat. It is commonly made from materials like polyolefin, PVC, or fluoropolymers, each offering unique properties suitable for different applications. The primary function of shrink tubing is to provide a protective covering for wires, cables, connectors, and other components, shielding them from moisture, chemicals, abrasion, and electrical interference.
Let’s start with the cutting process. Accurate cutting of shrink tubing is crucial to ensure a proper fit and functionality. Specialized tools such as tube cutters or sharp scissors are often used to make clean and straight cuts. When cutting, it’s important to measure the required length precisely to avoid wastage or insufficient coverage. For complex shapes or multiple components, a combination of cutting techniques may be employed to achieve the desired configuration.
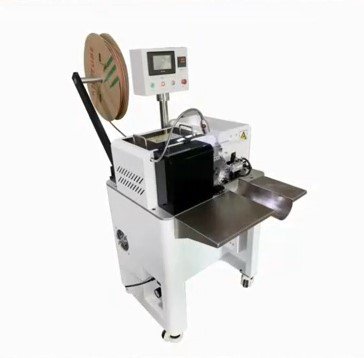
Now, onto the heating aspect, which is the key transformation step of shrink tubing. Heating can be done using various methods, including heat guns, ovens, or even open flames in some cases. However, heat guns are the most commonly used tool due to their portability and ease of control. The heat causes the tubing to contract uniformly around the object being covered, creating a tight and snug fit.

The temperature and duration of heating play a vital role in the quality of the shrink. Excessive heat or prolonged exposure can lead to over-shrinking, which may compromise the integrity of the tubing or the component it’s protecting. On the other hand, insufficient heat will result in a loose fit, failing to provide the desired protection and insulation. It’s essential to follow the manufacturer’s guidelines regarding the appropriate heating temperature and time for the specific type and size of shrink tubing being used.
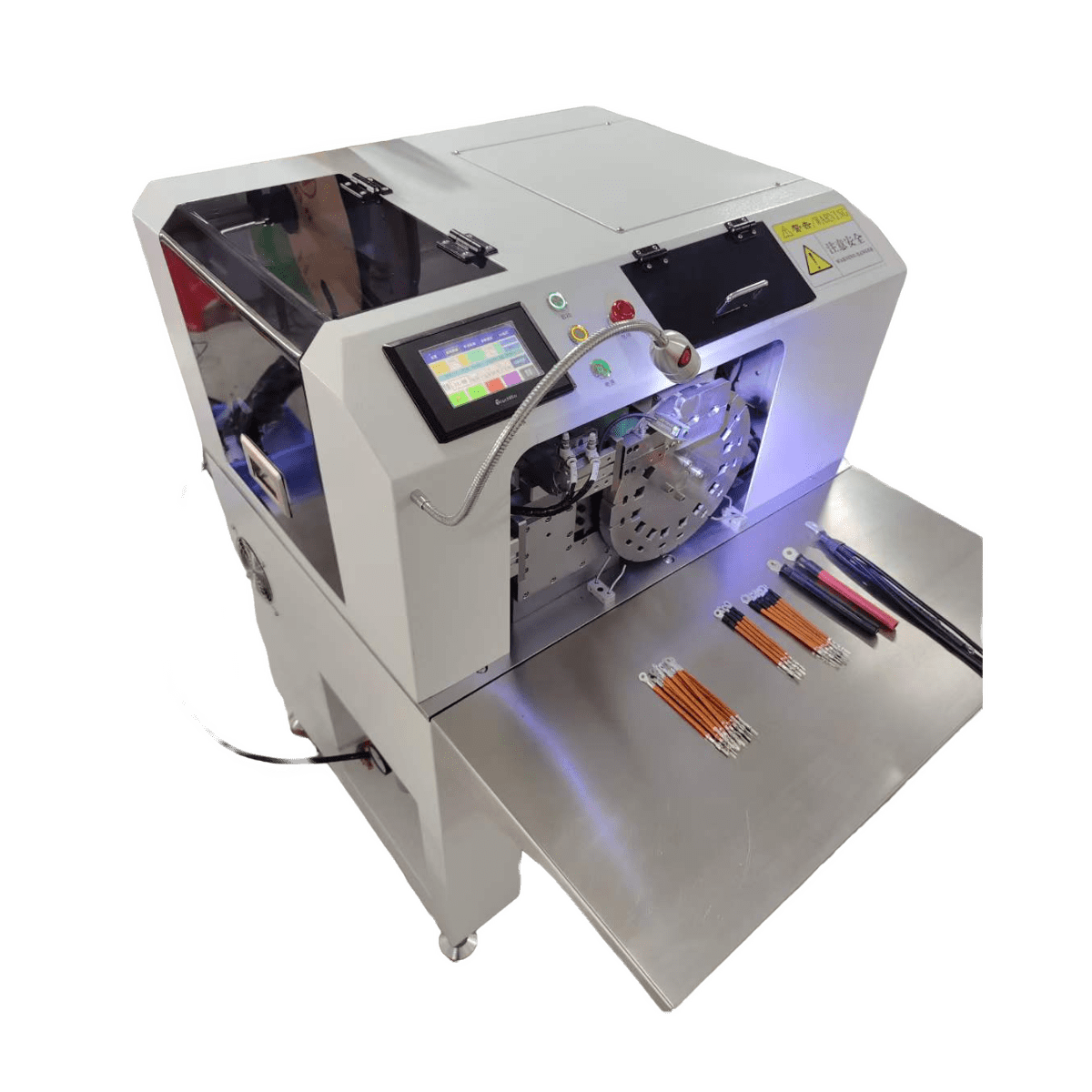
For example, when dealing with delicate electronic components, a lower temperature and shorter heating time might be necessary to prevent damage. In contrast, for heavy-duty applications where a stronger bond is required, a higher temperature and longer heating duration could be suitable.
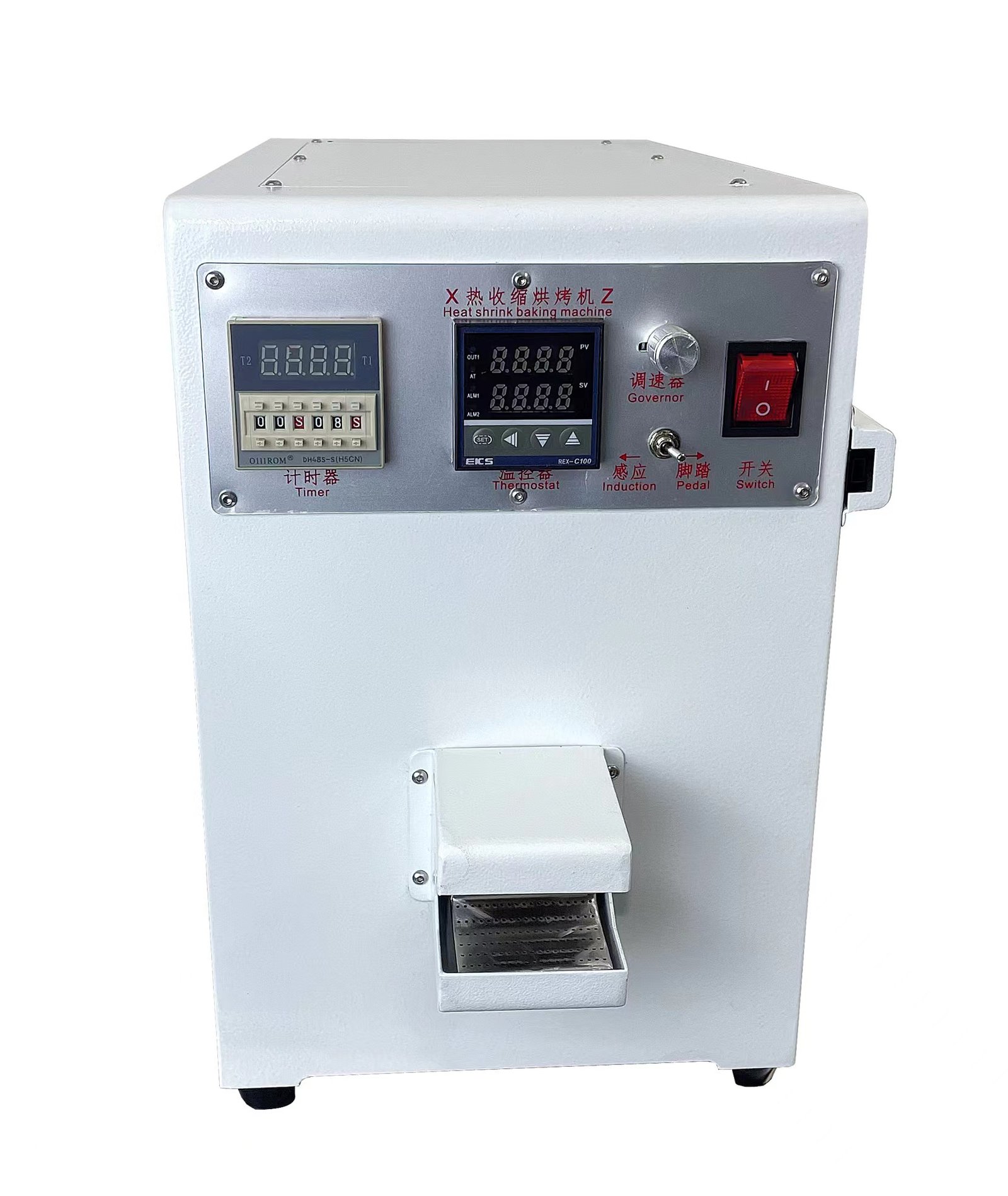
Shrink tubing also offers a wide range of colors and markings, which can be useful for identification and organization purposes. Different colors can be used to indicate the type of wire, voltage rating, or other important characteristics. This helps in quick and easy identification during maintenance and troubleshooting.
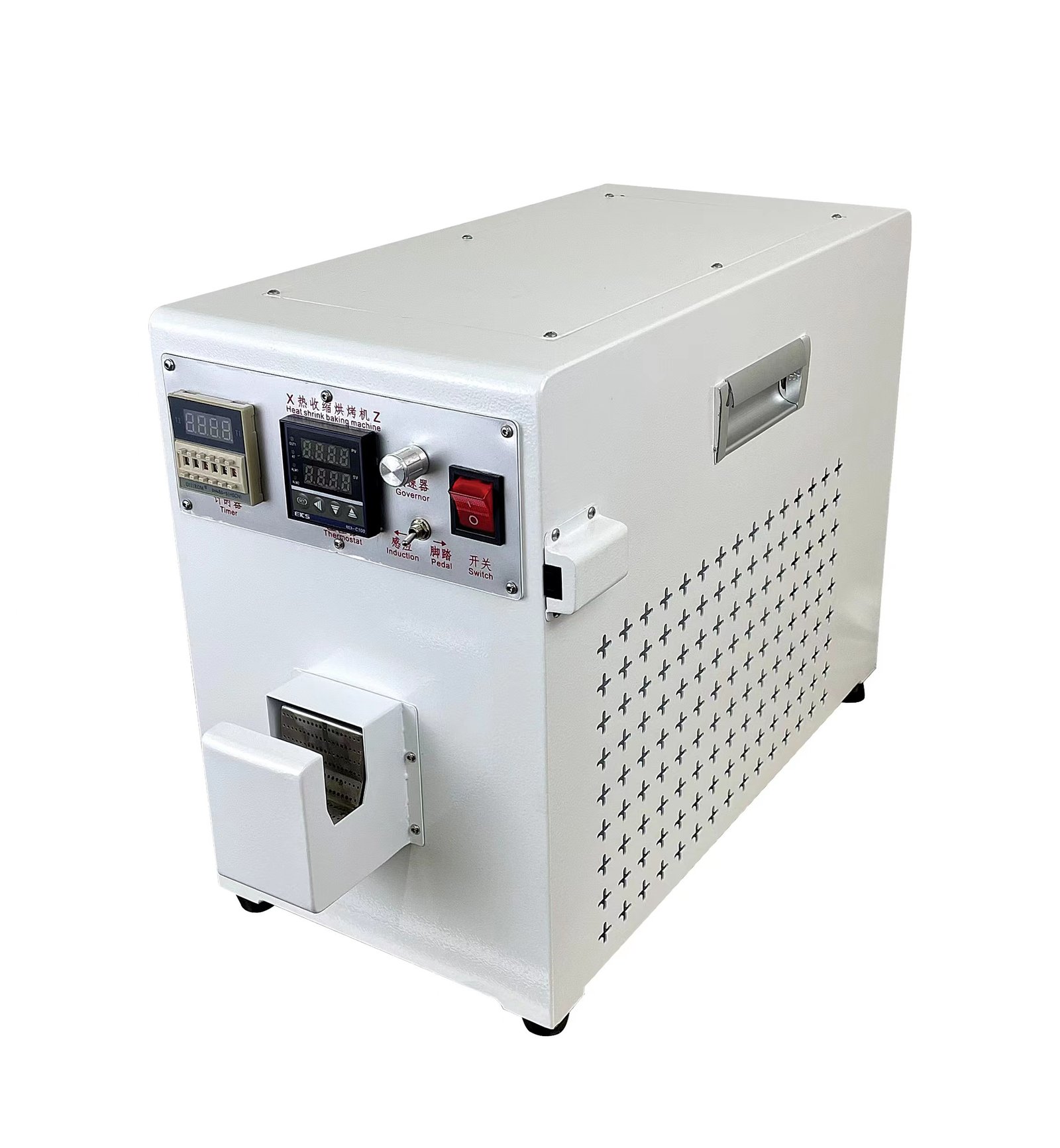
In addition to its use in electrical applications, shrink tubing finds its place in mechanical assemblies as well. It can be used to protect and seal pipes, rods, and other mechanical components from environmental factors and prevent loosening or movement.
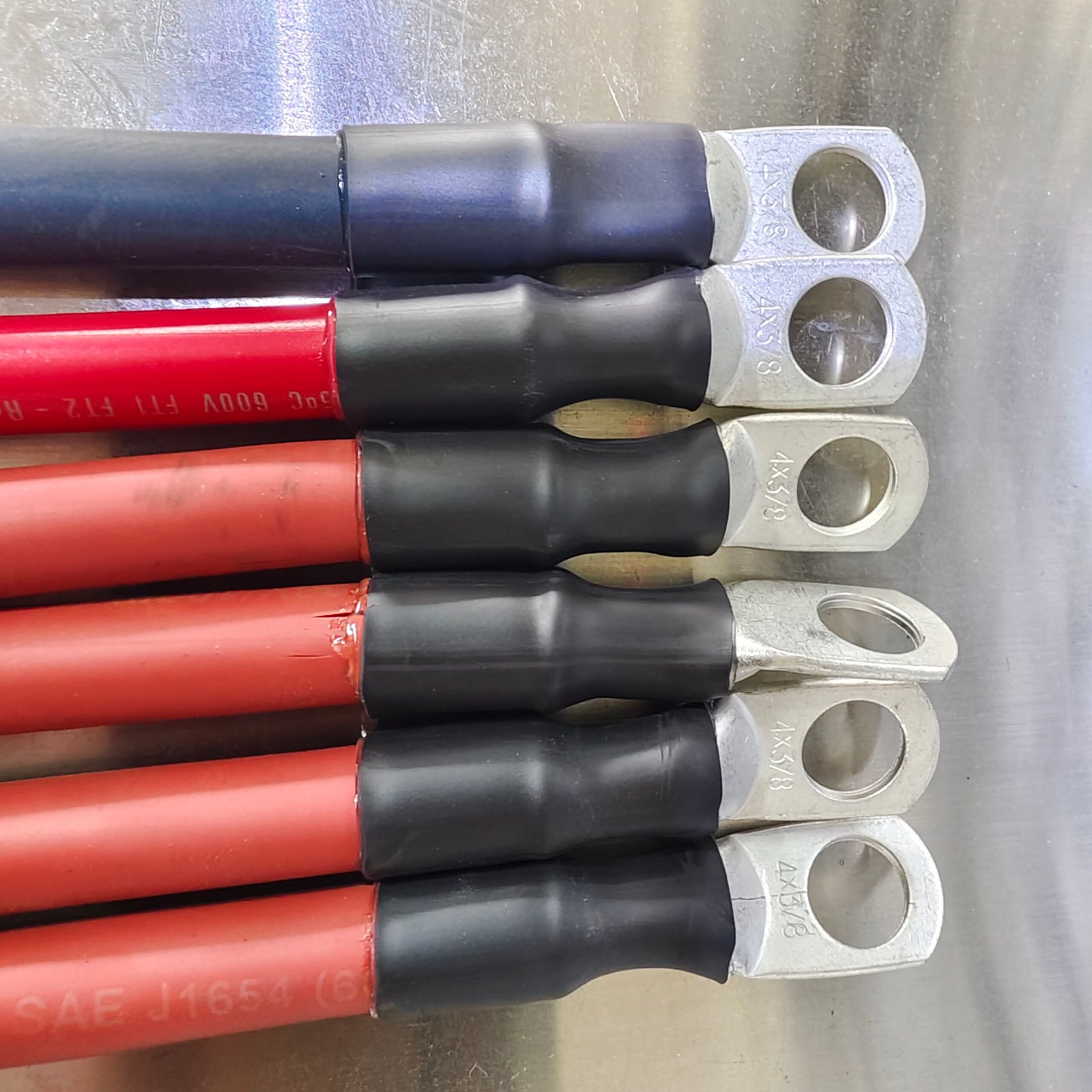
Furthermore, the advancements in shrink tubing technology have led to the development of specialized types such as dual-wall shrink tubing. This type features an inner adhesive layer that melts during the heating process, providing an extra layer of sealing and protection, especially in applications where watertight or airtight seals are crucial.
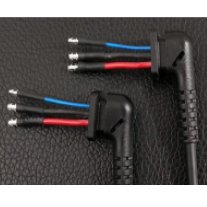
In conclusion, shrink tubing is a versatile and highly valuable component in numerous industries. The processes of cutting and heating, when executed accurately, ensure that shrink tubing fulfills its intended purpose effectively. Whether it’s in electronics, automotive, aerospace, or any other field that requires reliable protection and insulation, shrink tubing remains an essential solution. By understanding its properties, cutting techniques, and heating requirements, professionals can make the most of this remarkable material to enhance the performance and longevity of their systems and components.