In the world of manufacturing and fabrication, sleeve cutting plays a crucial role in various industries. Sleeve cutting involves the precise separation of materials to create sleeves of specific dimensions and shapes, which are used in numerous applications ranging from protective coverings to functional components. One of the advanced techniques employed in sleeve cutting is using a hot-melt cutter, which brings several advantages and requires specific skills and considerations.
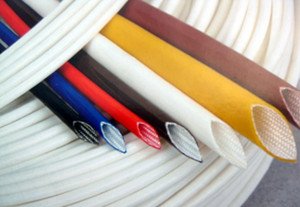
The hot-melt cutter is a specialized tool that operates on the principle of heat to achieve clean and accurate cuts. This method is particularly useful when dealing with materials that are sensitive to traditional cutting methods or require a seamless finish. The heat generated by the cutter melts the material at the cutting point, allowing for a smooth and precise separation without causing fraying or deformation.
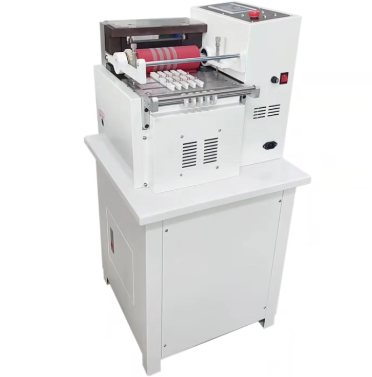
One of the key benefits of using a hot-melt cutter for sleeve cutting is the ability to work with a wide range of materials. From synthetic fabrics and plastics to certain types of composites, the hot-melt cutter can handle diverse substances with ease. This makes it a versatile option for industries such as textiles, automotive, and electronics, where sleeves made from different materials are in demand.
When it comes to the cutting process itself, several factors need to be taken into account. The temperature of the hot-melt cutter is a critical parameter that must be adjusted based on the material being cut. Different materials have different melting points, and using the incorrect temperature can lead to suboptimal cuts or even damage the material. Additionally, the speed at which the cutter is moved along the material also affects the quality of the cut. A controlled and steady movement ensures a consistent and clean edge.
Precision is of utmost importance in sleeve cutting, especially when the sleeves are intended for critical applications. Even the slightest deviation from the desired dimensions can render the sleeve unusable or compromise its functionality. The hot-melt cutter, when operated by a skilled operator, offers the ability to achieve tight tolerances and intricate shapes, meeting the stringent requirements of modern manufacturing.
Another advantage of the hot-melt cutter is the reduction in waste. Since the cutting process is precise and minimizes material distortion, there is less scrap generated compared to some other cutting methods. This not only saves on material costs but also contributes to a more sustainable and environmentally friendly manufacturing process.
However, it’s important to note that working with a hot-melt cutter requires proper safety precautions. The high temperatures involved pose a risk of burns, and operators must be equipped with appropriate protective gear. Additionally, the cutter itself needs to be maintained and calibrated regularly to ensure its performance and safety.
In conclusion, sleeve cutting with a hot-melt cutter is a cutting-edge technique that combines precision, versatility, and efficiency. As industries continue to demand higher quality and more complex sleeve designs, the use of this advanced cutting method is likely to become even more widespread. By understanding the principles, techniques, and safety considerations associated with hot-melt cutting, manufacturers can unlock its potential and produce sleeves that meet the exacting standards of today’s market.