Tape wrapping is a method of protecting and organizing the wires and cables that connect various electrical components in an automobile. Tape wrapping can prevent damage from abrasion, heat, moisture, chemicals, and noise, as well as improve the appearance and performance of the wiring harness.
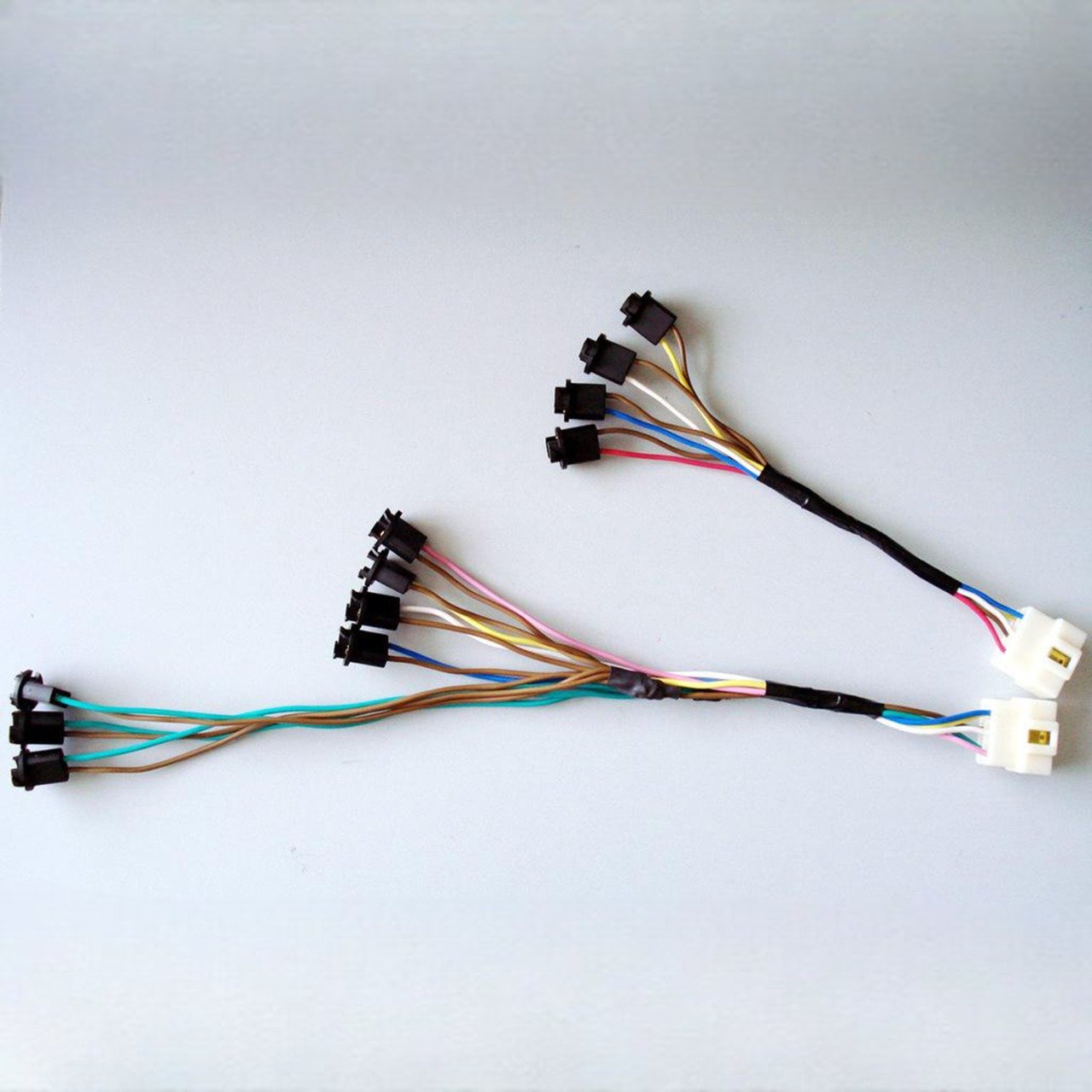
A wiring harness is a collection of wires, terminals, connectors, and other components that transmit electrical signals and power throughout the vehicle. A wiring harness can be found in the engine compartment, the dashboard, the doors, the trunk, and other places where electrical devices are installed. A wiring harness can have hundreds or thousands of wires, depending on the complexity and functionality of the vehicle.
Advantages of tape wrapping
• Flexibility: Tape wrapping can conform to any shape and size of the wiring harness, allowing for a snug and neat fit. Tape wrapping can also accommodate bends, curves, and branches in the wiring harness, without compromising the protection or insulation.
• Weight: Tape wrapping is lightweight and does not add much bulk to the wiring harness. This can reduce the fuel consumption and emissions of the vehicle, as well as improve the handling and performance.
• Ease of installation: Tape wrapping is easy to apply and remove, without requiring special tools or equipment. Tape wrapping can also be cut and spliced as needed, without affecting the integrity or functionality of the wiring harness.
• Versatility: Tape wrapping can provide different levels of protection and insulation, depending on the type and quality of the tape used. Tape wrapping can also be used for various purposes, such as bundling, sealing, marking, and noise reduction.
Tape wrapping consists of two main elements: the backing and the adhesive
The backing is the material that covers the wires and cables, while the adhesive is the substance that sticks the backing to the wiring harness. The backing and the adhesive can be made from different materials, each with its own characteristics and applications.
The most common types of backing materials for tape wrapping
• Polyvinyl chloride (PVC)
PVC is a plastic material that is widely used for tape wrapping due to its low cost, high durability, and good flexibility. PVC can resist abrasion, moisture, chemicals, and electrical currents, making it suitable for general purpose wrapping. PVC can also provide thermal and sound insulation, depending on the thickness and quality of the tape. However, PVC can also emit harmful gases when exposed to high temperatures or flames, which can pose a fire hazard or a health risk.
• Glass cloth
Glass cloth is a woven material made from glass fibers. Glass cloth can withstand high temperatures without melting or burning, making it ideal for wrapping wires in the engine bay or along the exhaust. Glass cloth can also resist abrasion, chemicals, and electrical currents, as well as provide thermal insulation. However, glass cloth can also be stiff and brittle, which can limit its flexibility and conformability.
• Fabric
Fabric is a textile material made from natural or synthetic fibers. Fabric can provide a soft and smooth surface for the wiring harness, which can reduce noise, vibration, and harshness (NVH) in the interior of the vehicle. Fabric can also be treated to be flame-retardant, water-resistant, or anti-static, depending on the application. However, fabric can also be prone to tearing, fraying, or fading, which can affect its durability and appearance.
The most common types of adhesive materials for tape wrapping
• Rubber
Rubber is a natural or synthetic material that has high elasticity and adhesion. Rubber can bond well to various surfaces and materials, making it versatile and adaptable. Rubber can also resist abrasion, moisture, and chemicals, as well as provide some thermal and sound insulation. However, rubber can also degrade over time, especially when exposed to heat, light, or oxygen, which can reduce its effectiveness and reliability.
• Acrylic
Acrylic is a synthetic material that has high strength and stability. Acrylic can withstand high temperatures and harsh environments, making it suitable for wrapping wires in the engine compartment. Acrylic can also resist abrasion, moisture, chemicals, and electrical currents, as well as provide thermal and sound insulation. However, acrylic can also be hard and rigid, which can limit its flexibility and conformability.
• Silicone
Silicone is a synthetic material that has high flexibility and adhesion. Silicone can conform to any shape and size of the wiring harness, allowing for a snug and neat fit. Silicone can also withstand high temperatures and harsh environments, making it suitable for wrapping wires in the engine bay or along the exhaust. Silicone can also resist abrasion, moisture, chemicals, and electrical currents, as well as provide thermal and sound insulation. However, silicone can also be expensive and difficult to remove, which can affect its cost-effectiveness and maintainability.
Tape wrapping can be done manually or automatically
Manual tape wrapping involves wrapping the tape around the wiring harness by hand, using a dispenser or a cutter. Manual tape wrapping can be more flexible and customizable, but also more time-consuming and labor-intensive. Automatic tape wrapping involves wrapping the tape around the wiring harness by a machine, using a feeder or a roller. Automatic tape wrapping can be more fast and efficient, but also more rigid and standardized.

Tape wrapping can be done in different ways, depending on the purpose and preference of the user.
Some of the common methods of tape wrapping
• Spiral wrapping
Spiral wrapping involves wrapping the tape around the wiring harness in a spiral or helical pattern, leaving some gaps between the layers of tape. Spiral wrapping can provide good flexibility and ventilation, as well as allow for easy access and inspection of the wires. However, spiral wrapping can also provide less protection and insulation, as well as create more noise and friction.
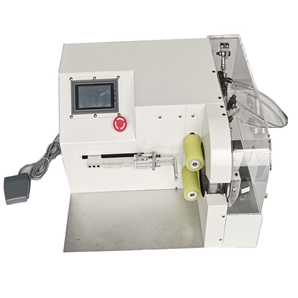
HH-345CLB 3:16 time of Pulling device and tractor
• Overlapping wrapping
Overlapping wrapping involves wrapping the tape around the wiring harness in a circular or linear pattern, overlapping the edges of the tape. Overlapping wrapping can provide better protection and insulation, as well as reduce noise and friction. However, overlapping wrapping can also reduce flexibility and ventilation, as well as create more bulk and weight.
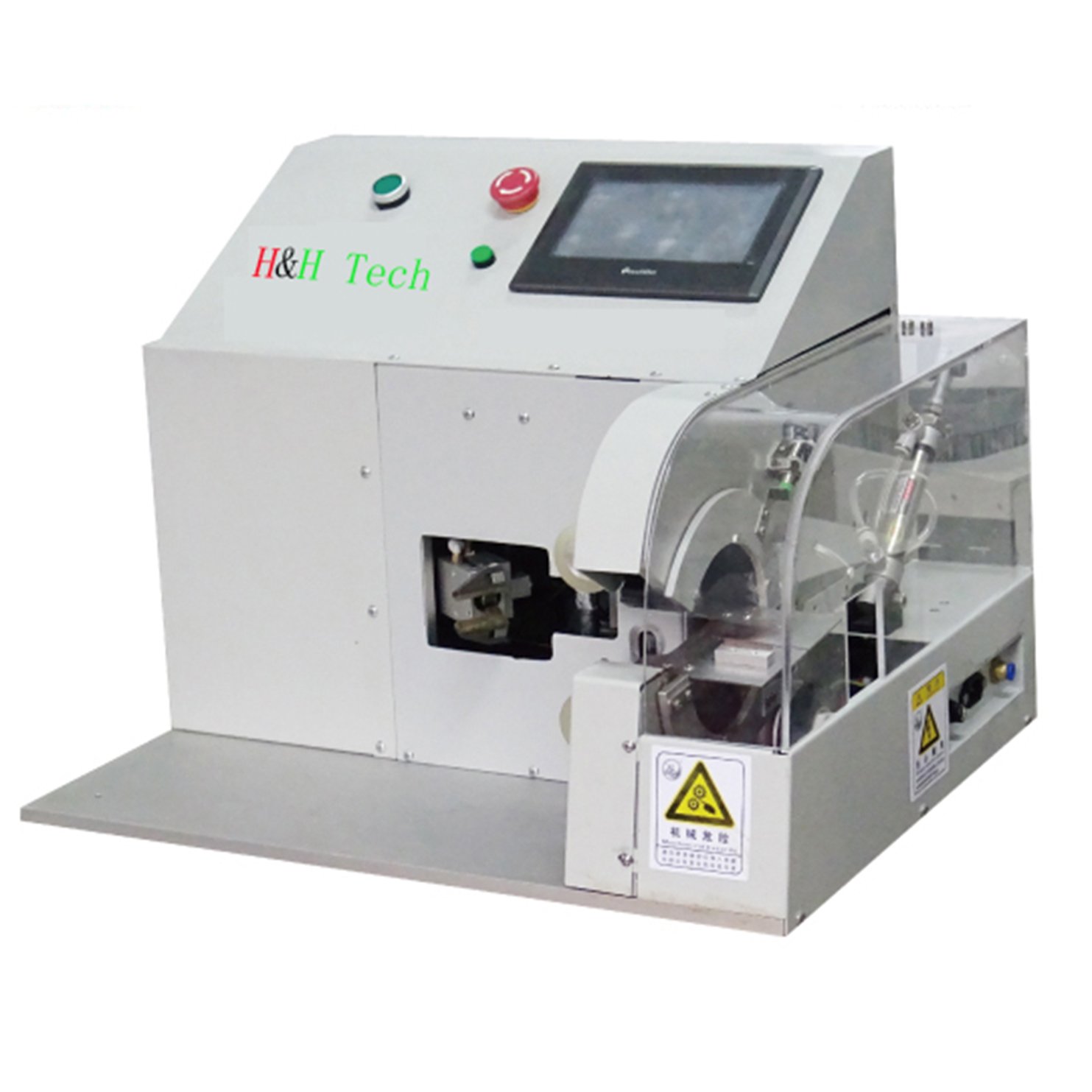
HH-345CL https://youtube.com/shorts/ZdNeRJ0PmJ4
• Spot wrapping
Spot wrapping involves wrapping the tape around the wiring harness in specific spots or sections, leaving some areas exposed. Spot wrapping can provide targeted protection and insulation, as well as save material and space. However, spot wrapping can also provide less coverage and consistency, as well as create more vulnerability and risk.
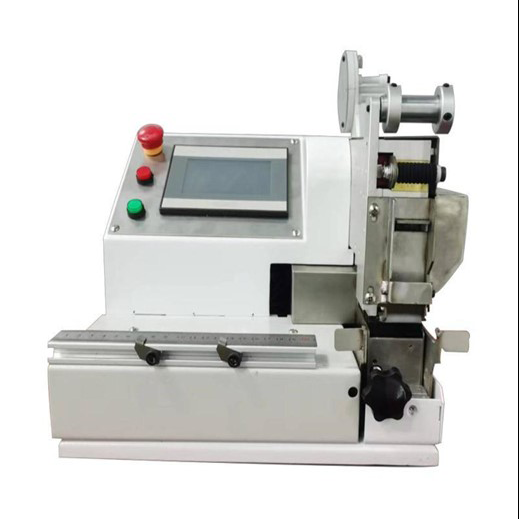
HH-345F Slide bar with fixture at customer’s site
HH-345F 40mm PVC tape on cable joints
Summary
Tape wrapping is a simple but effective way of protecting and organizing the wires and cables in an automobile. Tape wrapping can prevent damage from abrasion, heat, moisture, chemicals, and noise, as well as improve the appearance and performance of the wiring harness. Tape wrapping can also be done in different ways, depending on the type and quality of the tape, the size and complexity of the wiring harness, and the purpose and preference of the user. Tape wrapping is a method that can benefit both the vehicle and the driver.