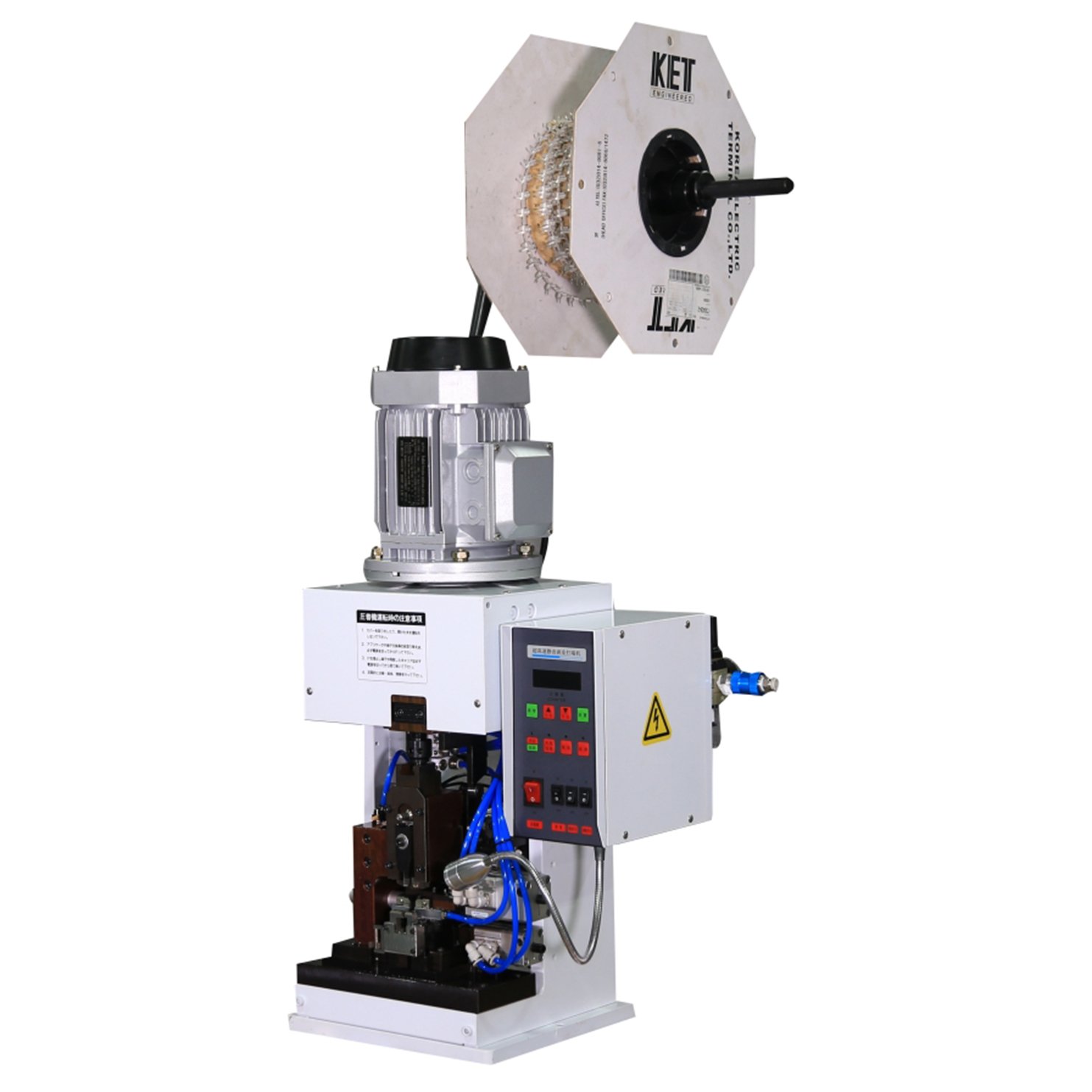
The problems that often occur in the process of adjusting the terminal machine are: insulation concealing, insulation protruding crimping, terminal deformation, some wire strands not crimped, wire strands breaking, wire strands concealing, terminal choking, insulation piercing.
Insulation Concealing
If the insulation is not seen vertically between conductor crimping and insulation crimping, it is called insulation concealing.
Causes of failure
1. The wire is not up to standard, and the insulation has a large flexibility.
2. Wire pulling force and wire feeding is not matched properly.
3. Cutting too long (e.g.stripping blades 42mm, cutter 42.2mm)
4. The lower cutter is too long or short. 5. The upper crimping blades is too long or short.
Solving measures
① Contact PQE, IE and IQC to negotiate the solution.
② Adjust the terminal feeding part to make the feeding in uniform speed and smoothly.
③ Install the suitable stripping blades.
④ Replace the lower cutter
⑤ Replace the upper cutter
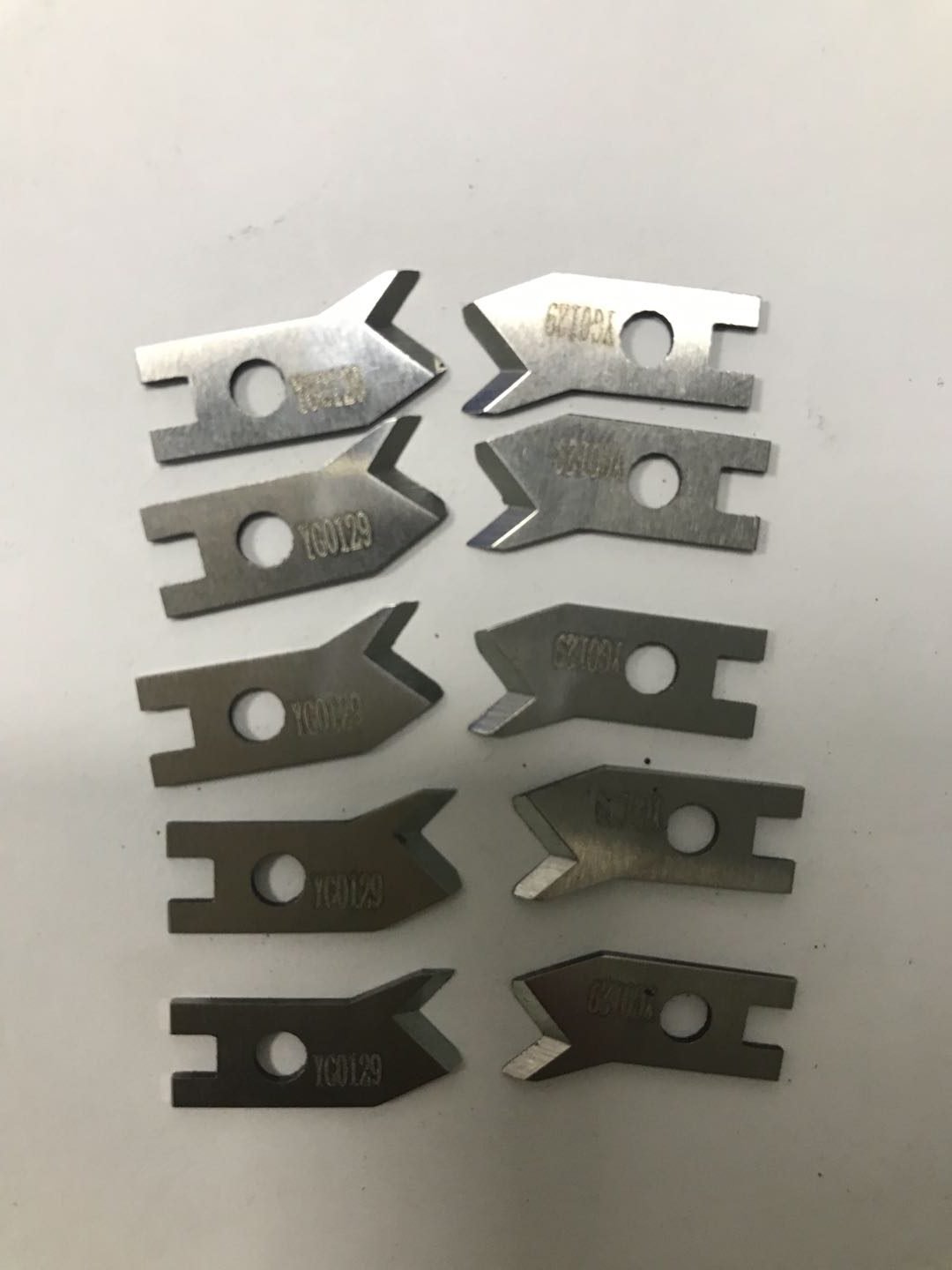
Insulation Protruding Crimping
The wire insulation is crimped into the conductor crimping part, it is called insulation protruding crimping.
Causes of failure
1. The wire is not up to standard, and the insulation has a large flexibility.
2. The size of the stripping blade is too large and the stripping is not neat.
3. The cutting blades is too long.
4. Wire is not clamping tightly.
5. Unstripped or stripping blades sandwiched with insulation debris. 6. The lower cutter is too long or short.
Solving measures
① Contact PQE, IE and IQC to negotiate the solution.
② Replacing cutting blades.
③ Replacing stripping blades
④ Adjust the wire clamping force ⑤ Clean the debris

Terminal Deformation
After the terminal is formed, the shape of the terminal is quite different and it is not easy to penetrate into receptacles.
Causes of failure
1. Terminal Feeding is not in place (wear of feeding claw, stop piece, pressing plate).
2. The blade is deformed or worn.
3. The clearance of the lower cutter is large, so that the terminal is stuck into the cutter.
4. The lower conductor anvil is too thin or too thick.
5. Upper blade chokes with terminal.
6. Terminal itself is deformed.
7. The pulling force is too large in the feeding process. 8. The upper cutter is too long.
Solving measures
① Replace with new spare parts.
② Replace the cutter.
③ Replace the lower cutter.
④ Replace the blade or grind the thick blade to fit.
⑤ Replace the upper blade.
⑥ Contact relevant personels to negotiate and solve the problem.
⑦ Adjust the tightness of terminal feeding.
⑧ Replace the lower cutter.
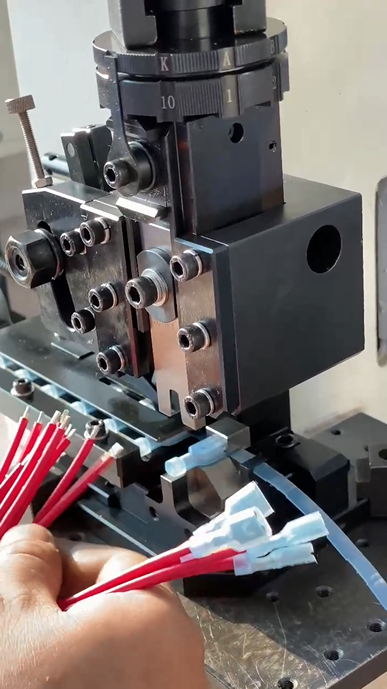
Some wire strands not crimped
After the terminal is crimped, part of the wire strands is attached to the surface of the terminal or visible on the outside of the terminal.
Causes of failure
1. Terminal feeding is not in place.
2. Wire feeding is not in place.
3. Terminal deformation.
4. Rough blade processing
5. The tip of the blade is too long or short.
6. The feeding fixture is not matched with the terminal machine.
7. The upper crimping blade is too long or short.
8. The lower cutting blade is too thick or thin. 9. The pressing spring is not in place.
Solving measures
① Adjust the feeding claw to the appropriate position.
② Adjust the feeding angle.
③ Check out the cause of deformation and solve it.
④ Replace the blade.
⑤ Replace the blade.
⑥ Balancing feeding fixture and the terminal machine.
⑦ Replace the upper crimping blades or grind off the tip part.
⑧ Replace lower cutting blade or grind it.
⑨ Adjust the position of pressing spring.
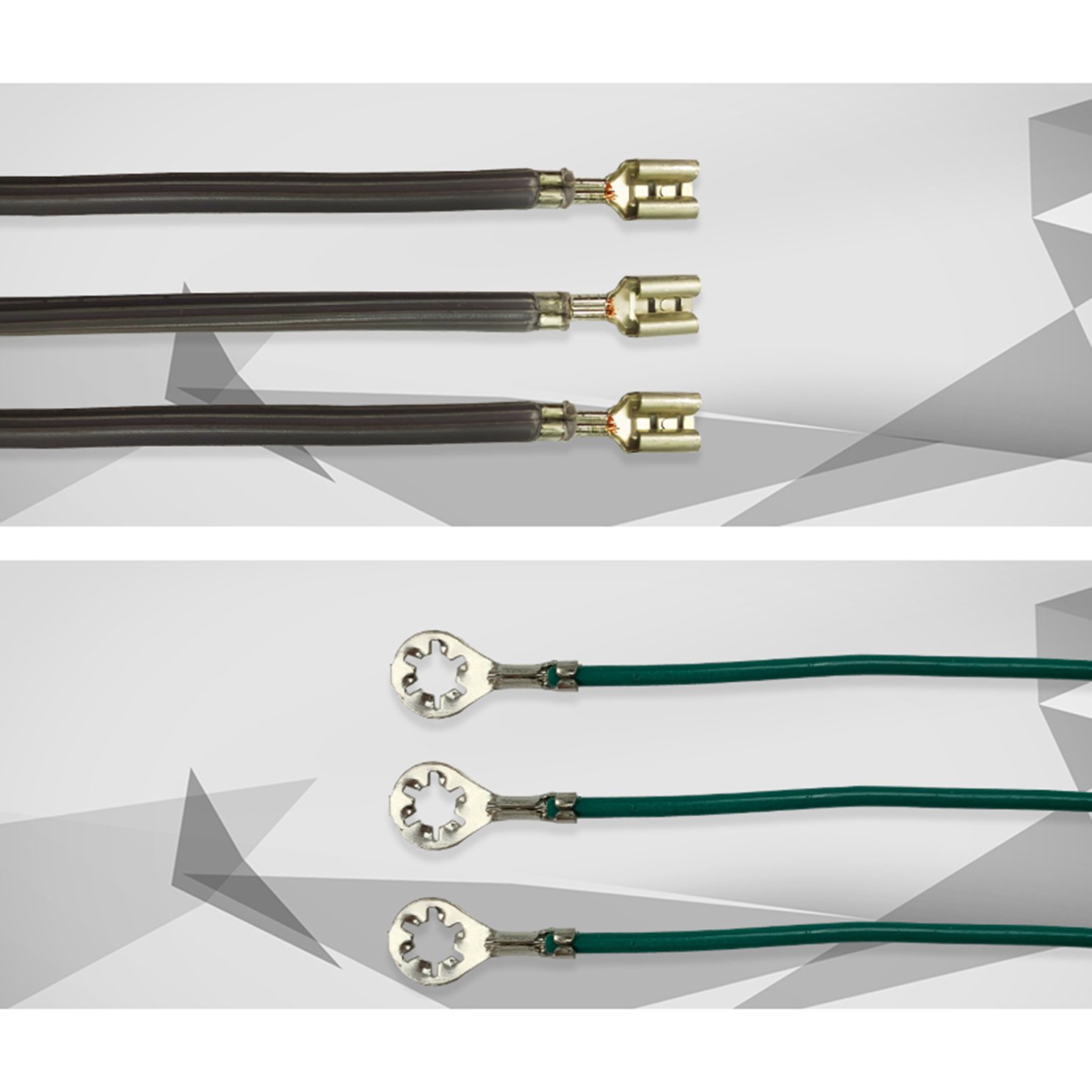
Wire strands breaking
The length of wire strands is not same.
Causes of failure
1. Cutting off when stripping.
2. The upper conductor crimping blade is too thick.
3. Conductor crimping is too deep.
4. The crimping edge of the blade is narrow.
5. The upper crimping blade is too short. 6. The upper crimping blade is too long.
Solving measures
① Replace the stripping blade.
② Replace the upper conductor crimping blade.
③ Adjust to the appropriate height.
④ Replace the blade.
⑤ Replace the upper crimping blades.
⑥ Replace the upper crimping blades.
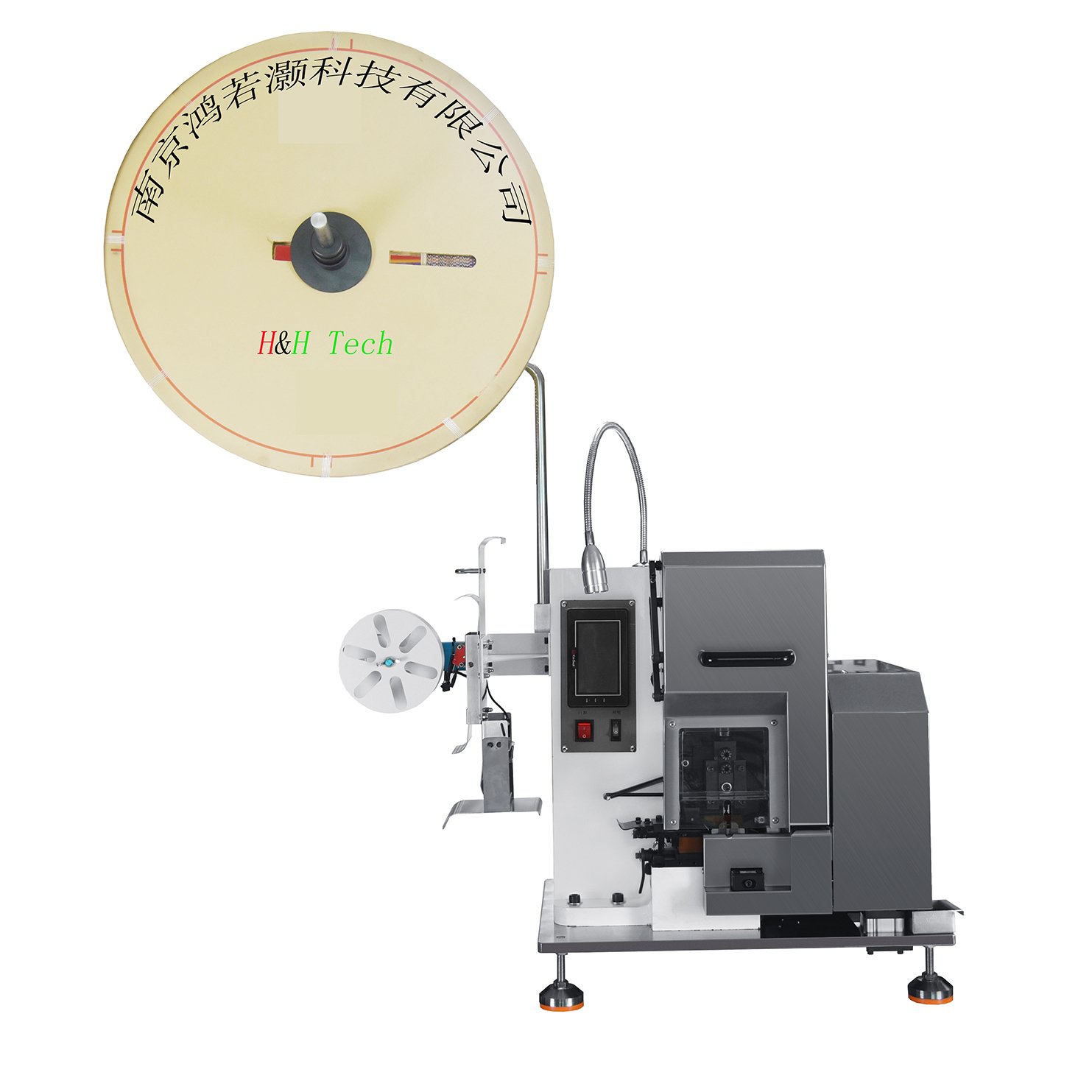
Wire strands concealing
The wire conductor can not be seen on the upper part of the terminal.
Causes of failure
1. Stripping is too long or too short.
2. The front and rear position of the terminal machine is not adjusted well.
3. Uneven shrinkage of wire insulation.
4. The stripping blades is too long.
5. Gap on cuting blades. 6. The stripping blades has a large edge.
Solving measures
① Adjust the thickness of the stripping blade.
② Adjust the terminal machine to the appropriate position.
③ Contact relevant personels to negotiate and solve the problem.
④ Replace the stripping blade.
⑤ Replace the cutter.
⑥ Replace it with a suitable stripping blade.
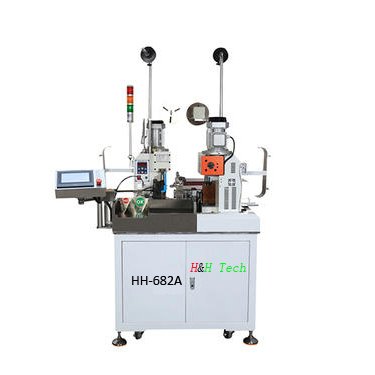
Terminal choking
The terminal is easily stuck in the blade or cutter.
Causes of failure
1. The blade is deformed, worn, or the straight part is too long.
2. Terminal deformation.
3. Cutter wear and large clearance. 4. The crimping edge of the blade is too narrow.
Solving measures
① Replace the blades.
② Change the terminal or find out the cause of its deformation and solve it.
③ Replace the cutter.
④ Replace the blades.
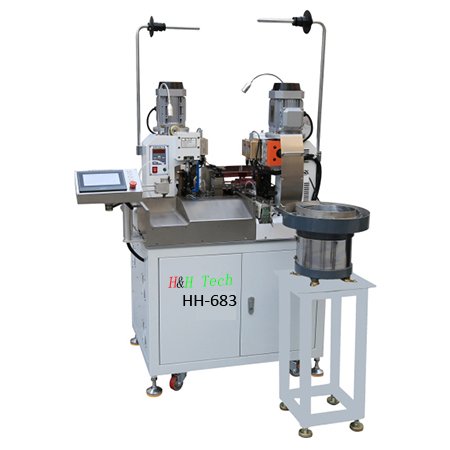
Insulation piercing
The wings of the terminal pierce into the insulation.
Causes of failure
1. Thickness of lower cutting blades.
2. The upper crimping blade is too short or too long.
3. The upper and lower blades are not long enough.
4. The feeding terminal is not in place.
5. Terminal itself is deformed.
6. The crimping edge of the blade is too narrow.
7. The pressing spring is not in place. 8. Large outer diameter of wire.
Solving measures
① Replace or repair the lower cutter.
② Replace the upper crimping blades.
③ Replace the blades.
④ Adjust terminal feeding.
⑤ Replace the deformed terminal.
⑥ Replace the blades.
⑦ Adjust the pressing spring of feeding part to the proper position.
