At present, the wire harness terminals used in automotive connectors are mainly made of high-quality copper alloy stamping. In order to protect the terminal substrate from corrosion and optimize the terminal surface performance, the terminals are usually treated with different surface treatments, such as fog tin, reflux bright tin, tin lead, silver, gold and palladium-nickel flash gold, that is, terminal surface plating.
What is the function of terminal plating?
We know that there are two main roles of the terminal in wiring harness connection, one is to tighten with the plastic shell, and the other is to form an electrical connection with the matching terminal. Although the copper alloy has good mechanical properties, however, the electrical conductivity performance is not satisfactory. While the materials with good electrical conductivity generally have ordinary mechanical properties, such as tin, gold, silver and so on.
Therefore, the plating is extremely necessary to make the terminal have both acceptable electrical conductivity and mechanical properties.
Analysis of common terminal plating
Tin-plated terminal
Tin-plated terminal can generally achieve good environmental stability in use, and because of its low cost, it is widely used in the market, and the main surface treatment methods are dark tin, bright tin, hot tin and so on.
However, its shortcomings are also obvious,
Firstly, compared with other platings, its wear resistance is poor, the number of insertion and pullout cycles is less than 10 times;
Secondly, the contact performance will decrease with time and temperature, which is generally used in the environment below 125 ℃.
In the design of tin-plated terminals, high contact force and small displacement should be considered to ensure the stability of contact.

Silver-plated terminal
The advantage of silver-plated terminal is that it has good point contact performance and can be used continuously at 150 ℃ environment. But it is expensive, and it is easy to rust in the air in the presence of sulfur and chlorine. And it is harder than tin, and its resistance coefficient is slightly higher than or equivalent to tin. The potential electron transfer phenomenon can easily lead to the potential risk of the connector.

Gold-plated terminal
Gold-plated terminals have good contact performance and environmental stability of tin-plated and silver-plated terminals, as well as excellent friction resistance.
It is accompanied by its higher cost among the three, but not every terminal needs to be plated. When tin-plated terminals wear out because of low contact force, we can use gold-plated terminals instead.
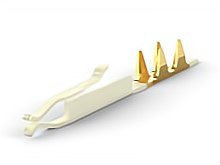

With the rapid development of the automobile industry and the requirements of the development direction of new energy and intelligence, various functional components in the automobile are also required to be intelligent, refined and reliable. The automobile connector is also gradually developing in the direction of high reliability, high density, miniaturization, high speed, standardization, integration and module.
Miniaturization means putting more modules in the limited space, that is, to achieve high density of the product.
Therefore, in the design of the connector, we have to consider the design of the force of insertion and pullout, which not only affects the complexity of the assembly and disassembly of connector, but also related to the electrical performance of the connector.
The application of terminal plating can not only reduce the corrosion of terminal material surface, but also improve the insertion force status.
To reduce the insertion force, it is necessary to reduce the friction force. There are three main factors that affect the friction coefficient between terminals: material, surface roughness and surface treatment.
The smallest surface roughness of different plating types is reflux bright tin and the largest is silver.
As to the insertion force of different surface treatment terminals, tin-lead is the largest, the smallest is gold, which is the comprehensive result of surface hardness and surface roughness, it can be seen that the insertion force performance of gold is better, tin-lead is relatively poor.
The pullout force of different electroplating is also tested that the pullout force of gold is better than that of tin and lead.
Therefore, the plating of the terminal not only protects the surface of the terminal material from corrosion, but also improves the insertion force status.
However, considering the performance-to-price ratio of functionality and economy, in addition to considering the design of the insertion force, we should also refer to the following conditions to select the appropriate terminal plating:
- Working conditions of the terminal withstanding the actual temperature;
- Environmentally friendly and non-corrosive;
- Featuring chemical stability;
- Ensure terminal contact;
- Reduce wear insulation;
- Low cost。
With the increasing complexity of the electrical environment of the whole vehicle and the arrival of the new energy era, only the continuous exploration of the manufacturing technology of parts and components can meet the rapid iteration of new functions.