I、Introduction to Nylon Tie Tying in Cable Assembly
Organization
Proper cable management with nylon ties helps keep cables neatly arranged and grouped. This reduces clutter and confusion, allowing for easier identification and access to specific cables when needed. For instance, in a data center with numerous cables running between servers and networking equipment, using nylon ties to bundle similar cables together can significantly improve the organization. It enables technicians to quickly locate and troubleshoot connections, minimizing downtime and increasing efficiency.
Safety
Effective cable management with nylon ties also enhances safety. Cables that are left loose can pose tripping hazards or get tangled, potentially causing damage to the cables and equipment. By securing cables with nylon ties, the risk of accidents is reduced. Moreover, proper cable routing and tying can prevent cables from coming into contact with heat sources or other potential hazards, reducing the likelihood of fire or electrical faults.
Functionality
In terms of functionality, well-managed cables using nylon ties ensure better signal transmission. Cables that are not properly organized can suffer from interference and signal loss. Nylon ties help maintain the correct separation and positioning of cables, optimizing their performance. Additionally, in environments where cables are subject to movement or vibration, such as in vehicles or industrial machinery, secure tying with nylon ties prevents cable disconnections or damage, ensuring continuous and reliable functionality.
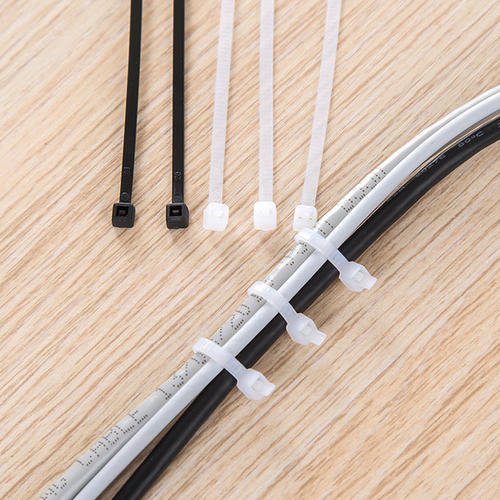
II、Understanding Nylon Ties
1. Types and Characteristics
Nylon ties come in several distinct types, each designed to meet specific needs. The standard nylon ties are commonly used for general-purpose cable bundling and offer moderate tensile strength and temperature resistance. They are made of high-quality nylon material that ensures durability and reliability.
Heavy-duty nylon ties, on the other hand, are engineered to handle more demanding applications. They boast a significantly higher tensile strength, capable of securely fastening larger and heavier cable bundles. These ties can withstand extreme temperatures, making them suitable for environments with harsh thermal conditions.
Releasable nylon ties provide added flexibility as they can be easily undone and reused. This feature is particularly useful in situations where cables may need to be accessed or reconfigured frequently.
The material properties of nylon ties contribute to their effectiveness. They are resistant to moisture, chemicals, and UV radiation, which prolongs their lifespan. The tensile strength of standard ties typically ranges from 18 to 50 pounds, while heavy-duty ones can exceed 120 pounds. Temperature resistance varies, with some nylon ties able to withstand temperatures from -40°F to 185°F without losing their integrity.
2. Advantages of Nylon Ties
Nylon ties offer several notable advantages. Their durability ensures long-term use without the risk of breakage or degradation. The flexibility of nylon allows for easy manipulation during installation, especially in tight spaces. Moreover, they are highly cost-effective compared to alternative cable management methods.
When compared to metal cable ties, nylon ties are lighter and less likely to cause damage to the cables they secure. They also do not conduct electricity, reducing the risk of electrical hazards. In contrast to Velcro cable wraps, nylon ties provide a more secure hold, especially in environments with significant vibration or movement.
Compared to cable clips or conduit, nylon ties are quicker and simpler to install, saving time and effort. Their low cost and wide availability make them an attractive option for both small-scale and large-scale cable management projects.
III、Preparing for Cable Assembly
1. Tools and Materials Needed
When preparing for cable assembly, several essential tools and materials are indispensable. Cutters are crucial for precisely trimming the nylon ties to the desired length. Pliers help in manipulating and tightening the ties for a secure hold. Different sizes of nylon ties are necessary to accommodate various cable diameters and bundling requirements. High-quality materials are of utmost importance as they ensure durability and reliability. Inferior materials may break or deteriorate over time, leading to potential cable disorganization and safety hazards. Choosing nylon ties made from superior nylon ensures they can withstand the environmental conditions and the tension applied.
2. Cable Organization and Planning
To assess the cable layout for optimal organization, start by visually inspecting the area where the cables will be routed. Consider the number and types of cables involved, as well as the available space. For example, if there are a large number of thick cables, more nylon ties and strategic placement will be needed. Measure the lengths and diameters of the cables to estimate the appropriate number of ties. Generally, it’s advisable to have a slightly higher number of ties than initially estimated to ensure sufficient support and stability.
The placement of nylon ties should follow a logical pattern. Group similar cables together and secure them at regular intervals to prevent sagging or tangling. In areas where cables are likely to experience movement or stress, place ties closer together for added reinforcement. It’s also important to leave some slack in the cables to accommodate future modifications or expansions. By carefully assessing the cable layout and determining the appropriate number and placement of nylon ties, you can achieve a neat, organized, and functional cable assembly.
IV、Techniques for Tying Nylon Ties
1. Basic Tying Method
First, hold the nylon tie in your hand. Pass the end of the tie through the locking mechanism. Then, wrap the tie around the cables you want to secure. Make sure to keep the tension consistent as you wrap. Avoid pulling too tightly, which could damage the cables, or too loosely, which might not provide a secure hold. Position the tie so that it evenly distributes the pressure across the cables. Finally, insert the end of the tie into the locking mechanism and pull it tight until you feel the appropriate tension.
2. Securing Multiple Cables
When dealing with multiple cables, start by sorting them based on their size and type. Group similar cables together. Begin by tying one end of the group with a nylon tie, then gradually add more ties along the length of the bundle. Make sure each tie is spaced evenly to maintain neatness and prevent tangling. You can also use larger-sized nylon ties for thicker bundles of cables.
3. Special Considerations and Tricks
For corners and bends, it’s crucial to leave some slack in the nylon tie to allow for movement without causing excessive stress on the cables. When handling different cable diameters, use multiple ties of appropriate sizes or adjust the tension accordingly. For example, for thicker cables, use a heavier-duty nylon tie and apply more tension. Another trick is to double-wrap the tie around smaller cables to increase the holding power. Always double-check the ties after installation to ensure a secure and tidy assembly.
V、Common Mistakes to Avoid
1. Over-Tightening or Under-Tightening
Over-tightening nylon ties can compress the cables too much, potentially damaging the insulation or even the conductors within. This not only weakens the cable’s performance but also increases the risk of electrical faults and signal disruptions. On the other hand, under-tightening allows cables to shift and move freely, which can cause tangling, abrasion, and intermittent connections.
To achieve the right balance, it’s essential to apply just enough tension to keep the cables securely in place without causing excessive deformation. A good rule of thumb is to be able to insert a finger between the tie and the cable without much force. Before tightening, visually inspect the cables to ensure they are laid out neatly and there are no kinks or twists that could be exacerbated by the tension.
2. Incorrect Cable Alignment
Proper alignment of cables before tying is of paramount importance. Misaligned cables can lead to uneven stress distribution along their length. This can cause premature wear and tear, especially in areas where the cables are subject to frequent movement or vibration. For instance, in automotive or industrial applications, incorrect alignment might result in cable breakage and subsequent system failures.
To avoid this, carefully arrange the cables in a parallel or organized manner, taking into account their natural paths and potential points of movement. Use guides or channels if available to keep the cables in the correct position. Aligning the cables also helps optimize the use of space and reduces the risk of interference between different cable groups. In conclusion, being aware of these common mistakes and taking the necessary precautions during nylon tie tying in cable assembly can significantly enhance the reliability and longevity of the cable management system.
VI、Testing and Inspection
1. Quality Checks
To inspect the tied cables for stability, neatness, and compliance with industry standards, the following steps can be followed. First, visually assess the overall arrangement of the cables. Ensure that they are neatly bundled and not tangled or crossed in an unorganized manner. Check for any loose or dangling cables that could indicate an unstable tie. Next, inspect the tension of the nylon ties. A proper tension should hold the cables firmly without excessive compression or slack. You can do this by gently pulling on the cables to check for any give or movement. Also, examine the ties themselves for any signs of wear, damage, or breakage. For compliance with industry standards, refer to the relevant specifications and guidelines. Check if the type and size of the nylon ties used are appropriate for the cable diameters and the application. Ensure that the spacing between the ties and the way they are fastened adheres to the prescribed standards.
2. Addressing Issues
When problems are identified during the inspection process, it’s essential to take prompt and appropriate corrective actions. If there are loose cables, re-tighten the nylon ties or add additional ties as needed. For damaged or broken ties, replace them immediately with new ones of the correct type and size. If the cables are not neatly arranged, carefully re-bundle them to achieve a more organized layout. In cases of non-compliance with industry standards, review the installation process and make the necessary adjustments to meet the requirements. It’s crucial to document all identified issues and the corrective actions taken for future reference and to ensure consistent quality in future cable tying and inspection processes. By promptly addressing these problems, the reliability and performance of the cable assembly can be maintained.
VII、Maintenance and Troubleshooting
1. Routine Maintenance
Periodic checks and maintenance are crucial for the sustained effectiveness of the nylon tie cable assembly. It is recommended to conduct inspections at least once every few months, depending on the environment and usage intensity. During these checks, visually inspect the ties for any signs of wear, fraying, or discoloration. Ensure that the cables remain securely fastened and are not showing any signs of loosening or shifting.
Also, check for any accumulation of dirt, dust, or moisture around the ties and cables, as these can accelerate deterioration. If the assembly is in an area with extreme temperatures or frequent vibrations, more frequent checks might be necessary.
In addition to visual inspections, it’s a good practice to gently tug on the cables to test the tightness of the ties. If there is any give or excessive movement, it might be time to re-tighten or replace the ties. Remember to keep records of each inspection, noting any issues found and the actions taken for future reference.
2. Dealing with Damaged or Loosened Ties
When dealing with damaged or loosened ties, prompt action is essential. If a tie is visibly cracked, broken, or has lost its tensile strength, it should be replaced immediately. To replace a tie, carefully cut the damaged one and remove it without causing further damage to the cables. Select a new tie of the appropriate size and type, and install it following the correct tying techniques described earlier.
For loosened ties, re-tightening might be sufficient. However, if the loosening is significant or has occurred multiple times in the same area, it could indicate a larger issue such as improper cable routing or excessive stress on the ties. In such cases, reevaluate the cable layout and make necessary adjustments.
It’s important to have a supply of spare nylon ties of various sizes on hand to facilitate quick replacements. And always ensure that the replacement ties are of high quality and suitable for the specific cable assembly application.
VIII、Conclusion
In this comprehensive exploration of nylon tie tying for cable assembly, we’ve covered numerous essential aspects. We began by understanding the organization, safety, and functionality benefits of proper cable management with nylon ties. We delved into the types and characteristics of nylon ties, their advantages over alternative methods, and the tools and materials needed for cable assembly preparation.
Techniques for tying nylon ties, including basic, multiple cable securing, and special considerations, were detailed. Common mistakes to avoid, such as over-tightening or under-tightening and incorrect cable alignment, were highlighted to ensure the longevity and reliability of the cable assembly. Testing and inspection procedures, as well as maintenance and troubleshooting tips, were also provided.
Mastering the art of nylon tie tying is of utmost importance for achieving efficient and reliable cable assembly. It not only enhances the organization and safety of the setup but also optimizes the functionality and performance of the cables.
We encourage readers to practice these techniques diligently and apply the knowledge gained to their cable assembly projects. With careful attention and skillful execution, you can create neat, secure, and high-performing cable assemblies that stand the test of time and meet your specific needs. So, go ahead and put your newfound skills to use for the best possible results.