I. Introduction to Shieldnet Cable Processing
Shieldnet cable processing plays a crucial role in modern industries due to its ability to ensure efficient signal transmission and protection against interference. The importance of this process cannot be overstated as it directly impacts the performance and reliability of various systems.
In numerous sectors such as telecommunications, aerospace, and automotive, shieldnet cables are indispensable. They facilitate seamless communication and data transfer, allowing for smooth operation of critical equipment and systems.

The four main segments of shieldnet cable processing – shieldnet cutting, shieldnet brushing, shieldnet twisting, and shieldnet assembly – each contribute significantly to the overall quality and functionality of the final product.
Shieldnet cutting is the first step, where precise cuts are made to ensure the correct length and shape of the cable. This requires advanced cutting tools and techniques to maintain accuracy and prevent damage to the shielding layer.
Shieldnet brushing is then carried out to clean and prepare the surface for further processing. It helps to remove any impurities or debris that might affect the electrical properties of the cable.
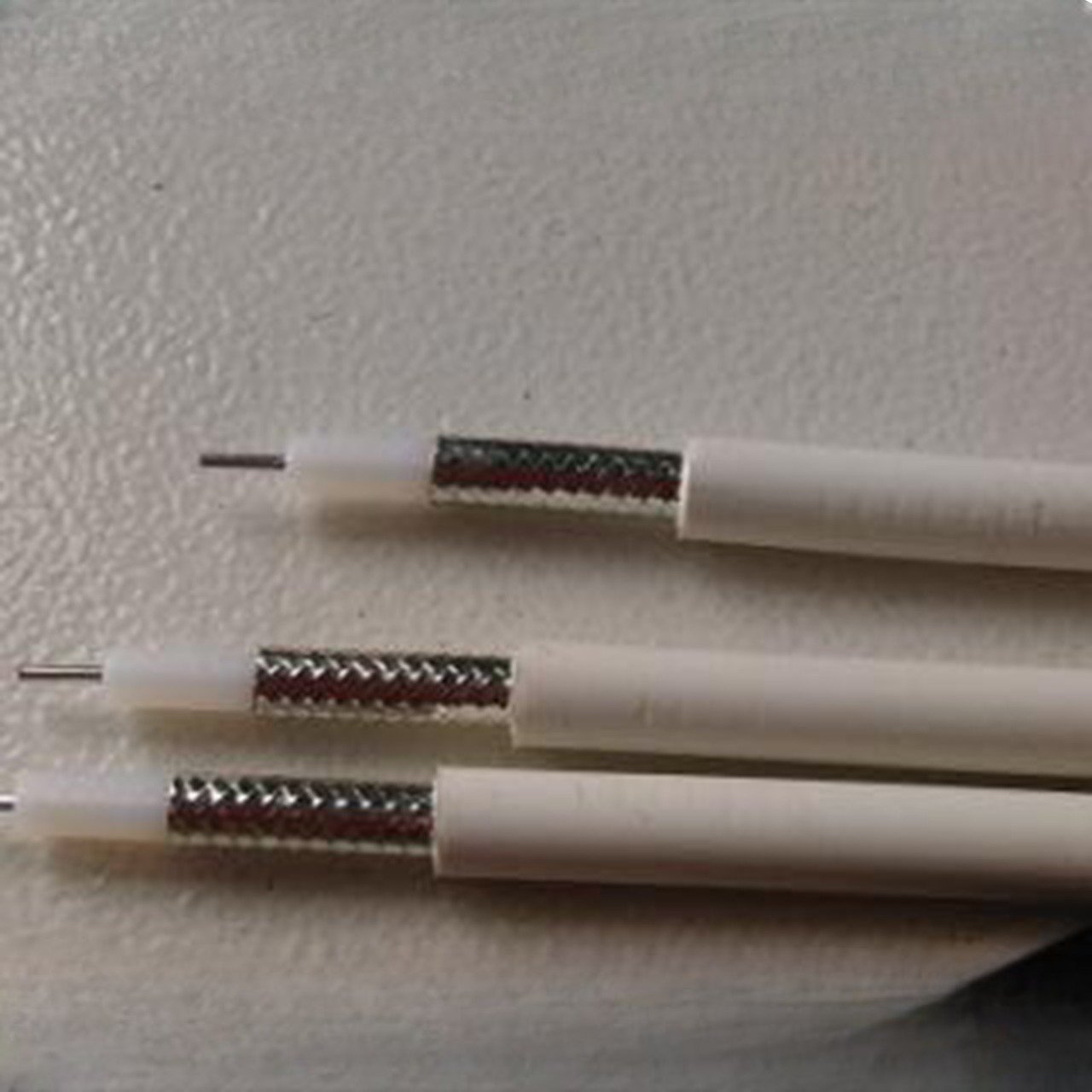
Shieldnet twisting is a crucial stage that enhances the cable’s flexibility and durability. By twisting the strands, the cable becomes more resistant to mechanical stress and ensures consistent signal transmission.
Finally, shieldnet assembly involves integrating the processed cable with other components to form a complete and functional system.
Overall, understanding and mastering these segments of shieldnet cable processing is essential for meeting the high standards and demands of today’s technological advancements.
II. Shieldnet Cable Cutting
2.1 Tools and Techniques for Shieldnet Cable Cutting
In the process of shieldnet cable cutting, specialized tools such as precision cable cutters and wire strippers are commonly employed. Precision cable cutters ensure clean and straight cuts, minimizing the risk of fraying or damaging the inner conductors and shielding layer. Wire strippers are used to remove the outer insulation precisely, allowing access to the inner components for subsequent processing. Laser cutting technology is also increasingly being utilized for its high precision and ability to handle complex shapes.
HH-3N25 https://youtube.com/shorts/FtG_JyHeL78 shieldnet cutting machine
2.2 Safety Precautions in Shieldnet Cable Cutting
Safety is of paramount importance during shieldnet cable cutting. Operators must wear appropriate personal protective equipment, such as safety glasses to protect the eyes from potential debris and insulated gloves to prevent electrical shock. The work area should be well-lit and free from clutter to avoid tripping hazards. It’s essential to ensure that the cutting tools are in good working condition and properly maintained to prevent malfunctions.
HH-3N25 https://youtube.com/shorts/rksocsHxyLI shieldnet cutting machine
2.3 Common Challenges and How to Overcome Them
One of the common challenges in shieldnet cable cutting is achieving consistent cut lengths, especially when dealing with large quantities of cables. This can be overcome by using calibrated cutting tools and fixtures. Another challenge is dealing with different types and sizes of cables, which may require adjusting the cutting parameters or using specialized adapters. Ensuring the sharpness of the cutting blades is crucial to prevent jagged cuts and damage to the cable.
HH-3N25 https://youtube.com/shorts/-gEfyuJ3lEc shieldnet cutting machine
2.4 Ensuring Accurate and Clean Cuts for Optimal Performance
To ensure accurate and clean cuts for optimal performance, it’s necessary to measure the cable precisely before cutting and mark the cutting points clearly. Regular calibration of the cutting tools and inspection of the cut surfaces for quality control are also important. Using high-quality cutting tools and maintaining them properly can significantly improve the cut quality, reducing the chances of signal interference and improving the overall performance of the shieldnet cable.
III.Shieldnet Cable Brushing
3.1 The Purpose of Shieldnet Cable Brushing
The main purpose of shieldnet cable brushing is to clean and prepare the surface of the cable. By removing dirt, oxides, and other contaminants, it enhances the electrical conductivity and reduces the risk of signal degradation. Additionally, brushing helps to create a smooth surface that promotes better adhesion during subsequent processing steps.
3.2 Types of Brushes Used for Shieldnet Cable Brushing
There are several types of brushes used for this process. Wire brushes with fine bristles are commonly employed to gently remove surface impurities without causing damage. Abrasive brushes may be used for more stubborn contaminants, but they require careful control to avoid excessive abrasion. Soft bristle brushes are preferred when the goal is to simply clean and polish the surface without altering its texture.
3.3 Proper Brushing Methods for Shieldnet Cable
The correct brushing method involves moving the brush along the length of the cable in a uniform and gentle manner. Applying too much pressure can deform the cable or damage the shielding. It’s important to use a back-and-forth motion to ensure thorough cleaning. Rotational brushing can also be effective, but again, care must be taken to avoid overdoing it.
3.4 Maintaining Cable Quality and Integrity during Brushing
To maintain the quality and integrity of the shieldnet cable during brushing, it’s crucial to select the appropriate brush type and brushing intensity based on the cable’s material and condition. Regular inspection of the cable for any signs of damage or deformation is necessary. Also, ensuring that the brush is clean and free from debris before use helps prevent introducing additional contaminants to the cable.
Overall, proper shieldnet cable brushing is a critical step in the processing that contributes significantly to the final performance and reliability of the cable.
IV. Shieldnet Cable Twisting
4.1 Machinery Utilized for Shieldnet Cable Twisting
Specialized machines, such as cable twisting machines, are employed for the shieldnet cable twisting process. These machines are designed to apply controlled torque and rotational speed to achieve the desired twist configuration. Some advanced models feature computerized control systems that allow for precise adjustment of twisting parameters to meet specific requirements.
4.2 Twisting Parameters and Their Significance
The twisting parameters, including the pitch (the distance between consecutive twists) and the degree of twist, play a crucial role in determining the cable’s performance. A shorter pitch and a higher degree of twist typically increase the cable’s flexibility and mechanical strength. However, excessive twisting can lead to increased capacitance and attenuation, affecting the signal transmission quality.
4.3 Impact of Twisting on Cable Properties
Twisting has a significant impact on the electrical and mechanical properties of the shieldnet cable. It improves the cable’s resistance to external electromagnetic interference, reducing signal loss. Additionally, it enhances the cable’s tensile strength and durability, making it more resilient in harsh environments. However, improper twisting can cause internal stress and distortion, potentially degrading the cable’s performance over time.
4.4 Quality Control Measures for Twisted Shieldnet Cables
Quality control is essential to ensure the twisted shieldnet cables meet the required standards. This involves inspecting the twist uniformity, checking for any kinks or deformations, and conducting electrical tests to verify the signal integrity. Regular calibration of the twisting machinery and training of operators are also important aspects of maintaining quality control.