I. The principle of Ultrasonic Welding
Ultrasonic welding is a common process of automobile wire harness welding at present, and the principle is that the surface of welding material is reassembled by high-frequency vibration.
Ultrasonic welding has the advantages of low energy consumption, no pollution, firm welding, excellent conductivity and low internal resistance, and does not change the chemical properties of the weldment.

II. Advantages of ultrasonic wire harness welding
1. Short welding time, high efficiency, high speed and energy saving.
2. The characteristics of non-melting and non-fragile conductor of welding materials.
3. After welding, the electrical conductivity is excellent, the strength is high, and the resistance is very low or close to zero.
4. No flux, gas or material is needed.
5. No spark and smoke in welding, environmental protection and safety.
6. Stable welding process and quality control.
III. Ultrasonic welding in automobile wire harness
The automobile wire harness is the network main body of the automobile circuit.
Without the wire harness, there would be no car circuit.
The traditional automobile wire harness refers to the components in which the contact terminals (connectors) made of copper are crimped with wires and cables, then the insulator or metal shell is molded on the outside, and the wiring harness is tied to form the components of the connecting circuit.
With the introduction of automotive electronic products and all kinds of communication equipment into the automobile, the requirements for the electrical signals transmitted by the automobile wire harness are becoming more and more stringent.
In order to meet these requirements of high-precision voltage and signal transmission, some special materials are used in the traditional wire harness manufacturing process, such as twisted pair, shielded wire, gold-plated terminal and so on.
However, it is still useless in most electronic control equipment and some special signals, such as CAN controller signal transmission line, airbag signal transmission line and some audio signal transmission line.
Although the existing terminal wire crimping process uses the above special materials, the signal is occasionally distorted or attenuated in the above signal transmission line.
1.Study on crimping process of terminal
For the automobile cable crimped by the traditional crimping process, it is found that a cavity is formed between the copper wire and the copper wire, and between the copper wire and the terminal wall.
In the traditional automobile wire harness production process, the contact terminal (connector) made of copper material is crimped with the wire, and only the copper wire is simply extruded to produce physical deformation of the copper wire, so it is possible to produce insufficient deformation of the copper wire. After the crimping of the terminal and the wire, the above holes are bound to be formed, and the existence of these holes is inevitable.
The existence of these holes will inevitably lead to the increase of the resistance coefficient of the crimping part and the decrease of electrical conductivity, thus affecting the transmission quality of current and signal, and then affecting the normal work of other electrical and electronic equipment.
At the same time, the quality defects caused by crimping in the process of wire harness production will lead to the reduction of service durability, and it is easy to heat and produce high temperature, which will form the hidden danger point of wire harness burning.
2.Comparative analysis of ultrasonic welding and terminal crimping
Ultrasonic welding is through the transistor function equipment to convert the electric frequency of 50 Hz into 20 kHz or 40 kHz, which is supplied to the converter, which converts the electrical energy into high-frequency mechanical vibration energy, and the voltage regulating device transmits the high-frequency mechanical energy to the welding head of the ultrasonic welding machine.
The vibration is transmitted to the two metal surfaces that need to be welded through the welding head, and the two metal surfaces rub against each other to form heat energy to make the metal melt. Under short pressure, the melt can produce strong molecular bonds when the bonding surface is solidified. Finally, the fusion between the metal molecular layers is formed. The whole cycle is usually completed in less than a second, but its welding strength is close to a connected material.
The traditional terminal crimping is a simple physical extrusion of the copper wire through the U-shaped part of the metal terminal, and the surface friction between the adjacent copper wire is used to ensure the connection between the wire and the terminal.
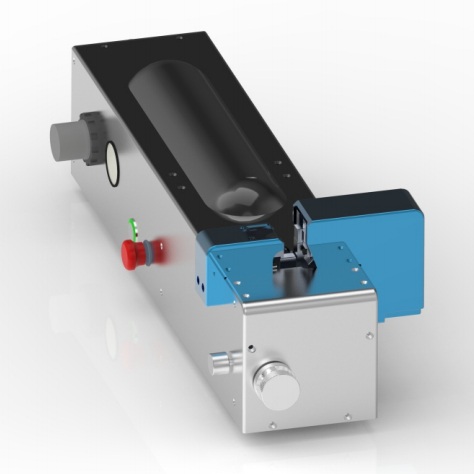
In fact, whether ultrasonic welded wires or terminals are in a moment shape at the crimping place, there are no loose core wires and broken or cracked core wires; moreover, the wires are not bent, but lead out in a straight line from the fusion.
Ultrasonic welding is through the melting of the adjacent metal surface to form the fusion between the metal molecular layers, which is equivalent to melting the adjacent metal into a whole. Compared with the adjacent copper wire is still an independent metal individual after terminal crimping, the density of the welding part is better. There will be no holes.
Ultrasonic welding features good electrical conductivity, low resistance coefficient, effectively durability improving, not easy to heat, and no quality hidden trouble, etc..
3. Analysis of test data of ultrasonic welding and terminal crimping
On the basis of the comparison of the appearance of the crimping joint and the analysis of the cross section, the pull-off force and electrical conductivity of the wires of the two crimping processes are tested.
Both ultrasonic welding and terminal crimping can meet the requirements in terms of pull-off force, but due to the difference of crimping process itself, there are often some quality defects such as voids in terminal crimping section, external leakage of core wire, damage of insulating layer and so on.
The voltage drop of ultrasonic welding is much lower than that of terminal crimping under the same conditions, so its electrical conductivity and signal transmission performance are much better than that of terminal crimping.
It can have at least the following 3 advantages.
①. It can avoid the hole formed by terminal crimping, improve the electrical conductivity and the stability of the whole electrical system.
②. Reduce the heat accumulation caused by contact resistance, which prevents the temperature rising and the hidden quality danger of wire harness burning.
③. Prevented from corrosion and oxidation of copper wire caused by external moisture, dust, oil and gas and other adverse factors, resulting in the decline of electrical conductivity and signal transmission distortion.
Conclusion
Based on the above research, the author thinks that for the lines with high signal requirements or high current, the ultrasonic welding between terminals and wires, wires and wires is very effective to improve the signal transmission quality or current transmission capacity. And it can also improve the stability of the automobile electrical system.